Waterproof connectors
Waterproof connectors are designed for use in wet or submerged environments to ensure secure and reliable connections without any leakage into or out of the equipment. .
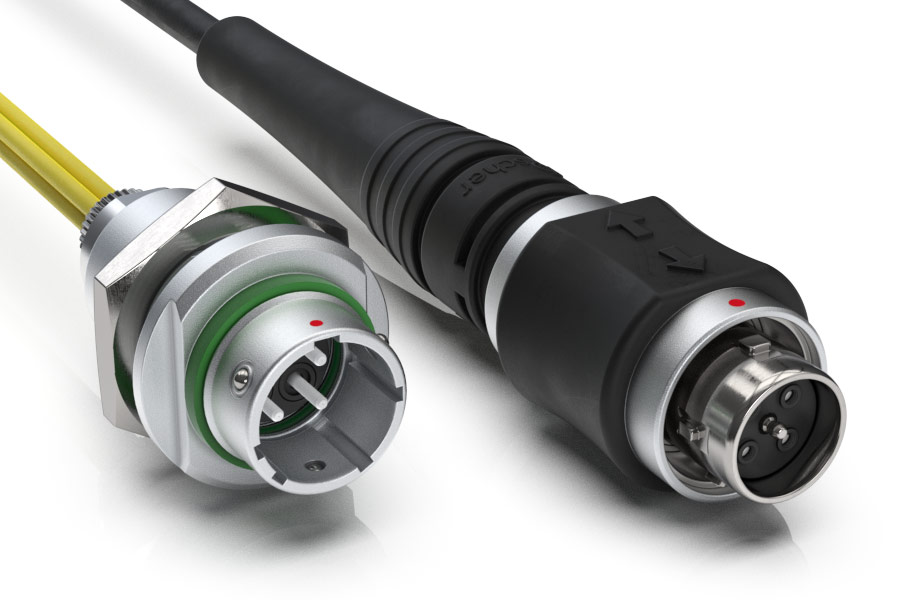
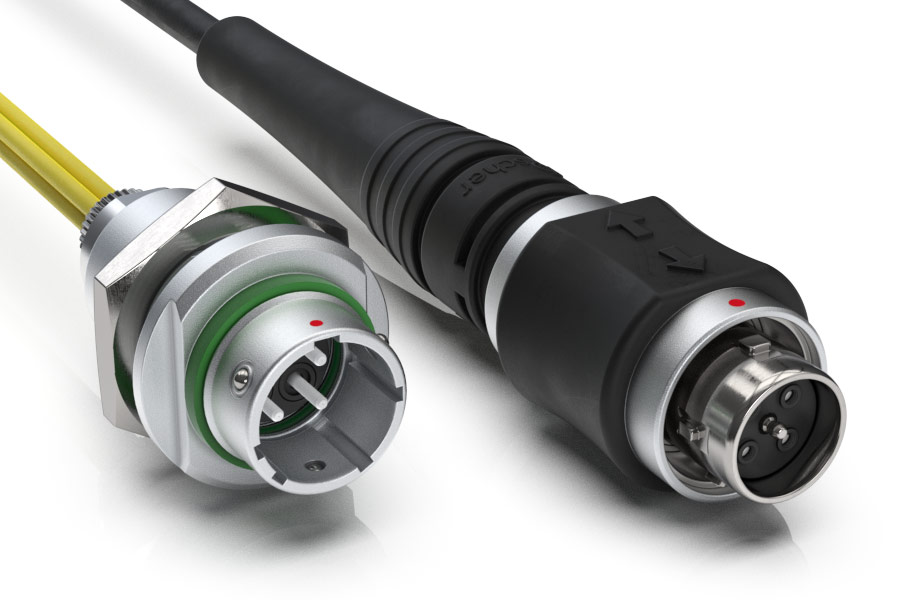
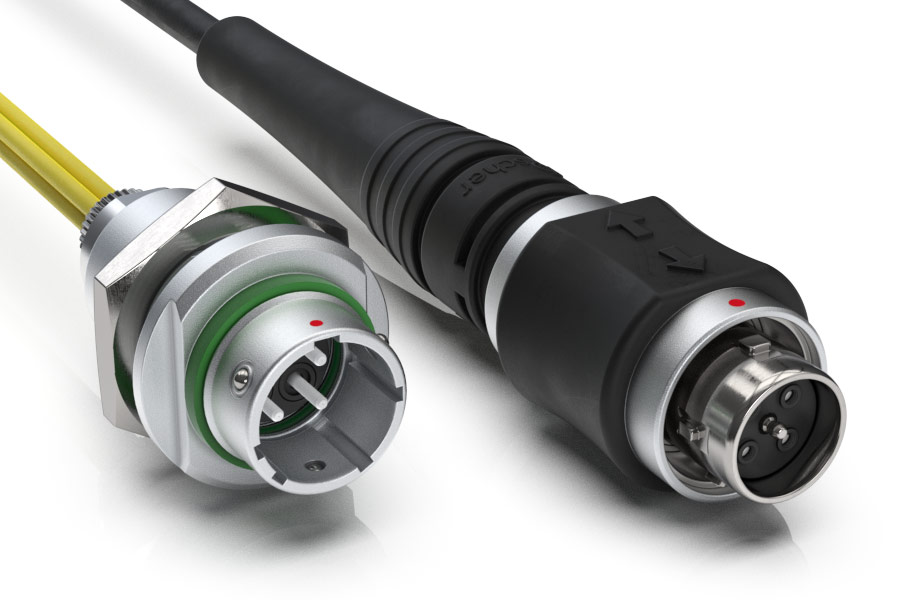
Sealing is a complex science, involving physical aspects such as mechanical design, materials & surface science, and fluid behavior.
Whether your devices and installations are exposed to rain, mud, intense water jets, salty mist, or deep-sea immersion, it’s crucial to have sealed connectivity solutions to maintain their long-term reliability.
Sealing is a complex science, involving physical aspects such as mechanical design, materials & surface science, and fluid behavior.
Whether your devices and installations are exposed to rain, mud, intense water jets, salty mist, or deep-sea immersion, it’s crucial to have sealed connectivity solutions to maintain their long-term reliability.
Sealing is a complex science, involving physical aspects such as mechanical design, materials & surface science, and fluid behavior.
Whether your devices and installations are exposed to rain, mud, intense water jets, salty mist, or deep-sea immersion, it’s crucial to have sealed connectivity solutions to maintain their long-term reliability.
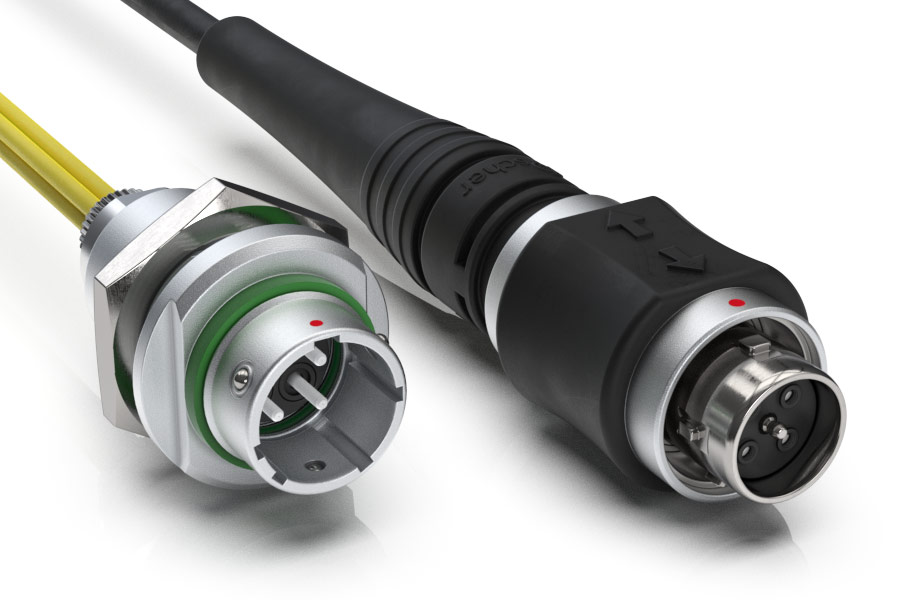
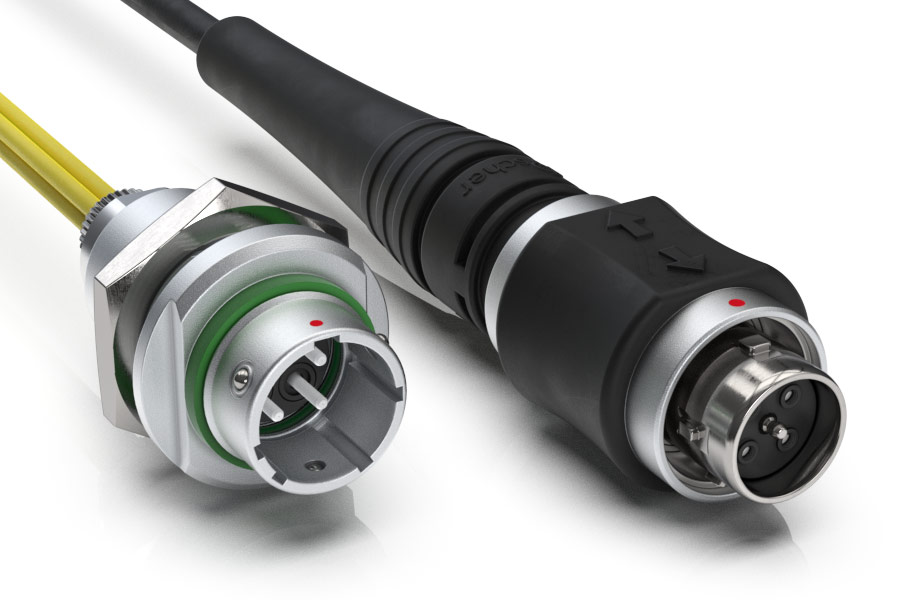
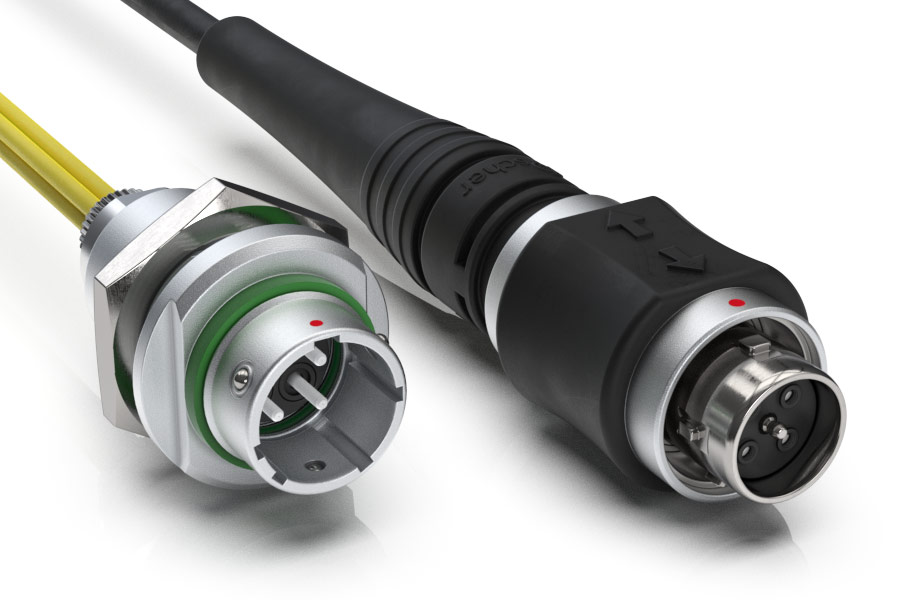
Sealing is a complex science, involving physical aspects such as mechanical design, materials & surface science, and fluid behavior.
Whether your devices and installations are exposed to rain, mud, intense water jets, salty mist, or deep-sea immersion, it’s crucial to have sealed connectivity solutions to maintain their long-term reliability.
Sealing is a complex science, involving physical aspects such as mechanical design, materials & surface science, and fluid behavior.
Whether your devices and installations are exposed to rain, mud, intense water jets, salty mist, or deep-sea immersion, it’s crucial to have sealed connectivity solutions to maintain their long-term reliability.
Sealing is a complex science, involving physical aspects such as mechanical design, materials & surface science, and fluid behavior.
Whether your devices and installations are exposed to rain, mud, intense water jets, salty mist, or deep-sea immersion, it’s crucial to have sealed connectivity solutions to maintain their long-term reliability.
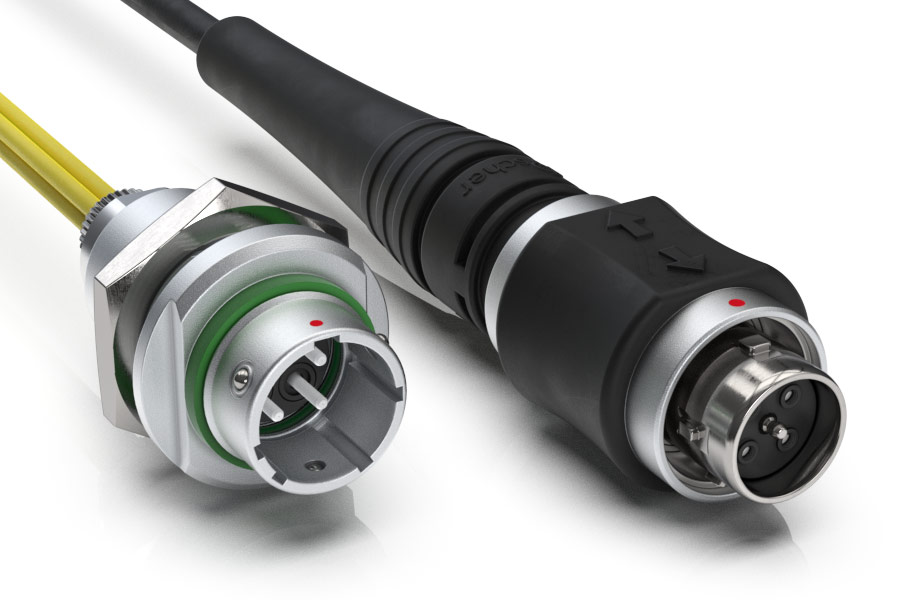
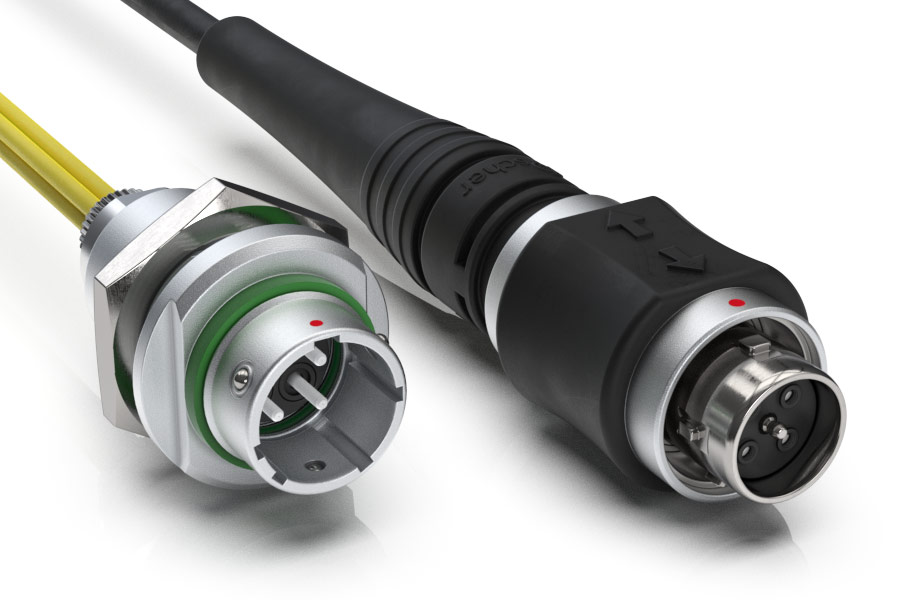
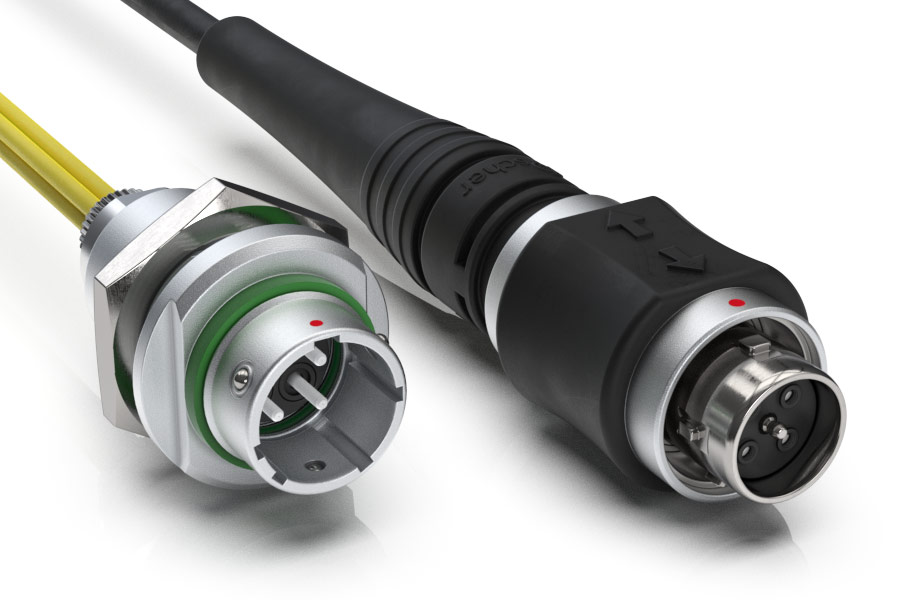
Sealing is a complex science, involving physical aspects such as mechanical design, materials & surface science, and fluid behavior.
Whether your devices and installations are exposed to rain, mud, intense water jets, salty mist, or deep-sea immersion, it’s crucial to have sealed connectivity solutions to maintain their long-term reliability.
Sealing is a complex science, involving physical aspects such as mechanical design, materials & surface science, and fluid behavior.
Whether your devices and installations are exposed to rain, mud, intense water jets, salty mist, or deep-sea immersion, it’s crucial to have sealed connectivity solutions to maintain their long-term reliability.
Sealing is a complex science, involving physical aspects such as mechanical design, materials & surface science, and fluid behavior.
Whether your devices and installations are exposed to rain, mud, intense water jets, salty mist, or deep-sea immersion, it’s crucial to have sealed connectivity solutions to maintain their long-term reliability.
Sales request
Get STEP files and product information
Our waterproof connector solutions
Fischer Connectors’ worldwide reputation for sealing technology and expertise comes from the first high-quality sealed connector for industrial applications, which was developed in 1954 by Walter Werner Fischer.
When choosing a waterproof connector, it’s important to note that not all IP68 ratings are the same. While some IP68-rated connectors may only be suitable for 1.5 meters for 30 minutes, Fischer Connectors offers some of the toughest IP68-rated waterproof connectors in the industry, tested up to 20 meters for 24 hours (or more upon request). These connectors are designed to extreme conditions in harsh environments.
Fischer Connectors’ worldwide reputation for sealing technology and expertise comes from the first high-quality sealed connector for industrial applications, which was developed in 1954 by Walter Werner Fischer.
When choosing a waterproof connector, it’s important to note that not all IP68 ratings are the same. While some IP68-rated connectors may only be suitable for 1.5 meters for 30 minutes, Fischer Connectors offers some of the toughest IP68-rated waterproof connectors in the industry, tested up to 20 meters for 24 hours (or more upon request). These connectors are designed to extreme conditions in harsh environments.
Fischer Connectors’ worldwide reputation for sealing technology and expertise comes from the first high-quality sealed connector for industrial applications, which was developed in 1954 by Walter Werner Fischer.
When choosing a waterproof connector, it’s important to note that not all IP68 ratings are the same. While some IP68-rated connectors may only be suitable for 1.5 meters for 30 minutes, Fischer Connectors offers some of the toughest IP68-rated waterproof connectors in the industry, tested up to 20 meters for 24 hours (or more upon request). These connectors are designed to extreme conditions in harsh environments.
Key features
- IP68 sealing up to -20m/24h mated and unmated
- High corrosion resistance (salt mist, sterilization, chemicals)
- Compliance with multiple data-transfer protocols (USB 2.0, USB 3.2, Ethernet, Single Pair Ethernet, Audio/UHD Video)
- Lightweight and compact solutions
- Technical support and assistance
We assist and guide you in carefully selecting solutions with the appropriate level of environmental and hermetic sealing for your specific device and operating conditions. Our product tests are conducted according to the highest standards.
We assist and guide you in carefully selecting solutions with the appropriate level of environmental and hermetic sealing for your specific device and operating conditions. Our product tests are conducted according to the highest standards.
We assist and guide you in carefully selecting solutions with the appropriate level of environmental and hermetic sealing for your specific device and operating conditions. Our product tests are conducted according to the highest standards.
Our product range
Our product range
Our product range
Need other features?
Our custom connector capabilities will help you meet your needs.
Learn more about waterproof connectors
When designing your equipment, choosing the right connectivity solutions with the right type of sealing early in the process is critical for the commercial success and durability of your product.
Three major application groups exist that require different sealing levels, and therefore call for different solutions.
When designing your equipment, choosing the right connectivity solutions with the right type of sealing early in the process is critical for the commercial success and durability of your product.
Three major application groups exist that require different sealing levels, and therefore call for different solutions.
When designing your equipment, choosing the right connectivity solutions with the right type of sealing early in the process is critical for the commercial success and durability of your product.
Three major application groups exist that require different sealing levels, and therefore call for different solutions.
Environmental sealing
In typical outdoor applications, one side of the waterproof connector might be exposed to rain, dust and other aggressive environments. The exposure is generally limited in time and pressure.
Fischer Connectors’ product range for these applications includes receptacles sealed in mated or unmated states; for example, styles DEU, DBEU, DBPU, etc., as well as plugs in association with sealed clamp sets. These products are designed to offer sealing up to IP68.
Hermetic sealing
Hermeticity is normally required for gas tightness in vacuum applications or pressurized vessels. These applications require a high level of sealing to prevent gas leaks over longer periods of time. Fischer Connectors’ styles DEE, DBEE, DBPE, etc., are designed specifically for hermetic sealing and undergo a 100% leak test.
Such waterproof connectors should be used in severe conditions like immersion for longer periods of time or exposure to strong water jets. They achieve an IP69K rating.
Environmental sealing
In typical outdoor applications, one side of the waterproof connector might be exposed to rain, dust and other aggressive environments. The exposure is generally limited in time and pressure.
Fischer Connectors’ product range for these applications includes receptacles sealed in mated or unmated states; for example, styles DEU, DBEU, DBPU, etc., as well as plugs in association with sealed clamp sets. These products are designed to offer sealing up to IP68.
Hermetic sealing
Hermeticity is normally required for gas tightness in vacuum applications or pressurized vessels. These applications require a high level of sealing to prevent gas leaks over longer periods of time. Fischer Connectors’ styles DEE, DBEE, DBPE, etc., are designed specifically for hermetic sealing and undergo a 100% leak test.
Such waterproof connectors should be used in severe conditions like immersion for longer periods of time or exposure to strong water jets. They achieve an IP69K rating.
Environmental sealing
In typical outdoor applications, one side of the waterproof connector might be exposed to rain, dust and other aggressive environments. The exposure is generally limited in time and pressure.
Fischer Connectors’ product range for these applications includes receptacles sealed in mated or unmated states; for example, styles DEU, DBEU, DBPU, etc., as well as plugs in association with sealed clamp sets. These products are designed to offer sealing up to IP68.
Hermetic sealing
Hermeticity is normally required for gas tightness in vacuum applications or pressurized vessels. These applications require a high level of sealing to prevent gas leaks over longer periods of time. Fischer Connectors’ styles DEE, DBEE, DBPE, etc., are designed specifically for hermetic sealing and undergo a 100% leak test.
Such waterproof connectors should be used in severe conditions like immersion for longer periods of time or exposure to strong water jets. They achieve an IP69K rating.
Underwater and high-pressure sealing
To withstand exposure for extended periods of time in liquids under high pressure, applications such as deep-submarine applications or pipeline-inspection equipment, and seismic-evaluation or drilling instruments in oil & gas, require waterproof connectors with special designs combining hermetic sealing with high-strength mechanical designs to guarantee safe and efficient operations.
Design engineers face special technical challenges for their marine and underwater applications such as autonomous and remotely operated underwater vehicles (ROV, AUV or UUV), which operate at depths where diving by humans is either impractical or dangerous.
Such demanding applications involved in immersion over long periods require ultra-sealed, watertight, cabled waterproof connectors that achieve an IP68 rating in both mated and unmated states.
Salt strongly increases water conductivity, so seawater and salt mist can act as an electrolyte, causing galvanic corrosion. Our IP68/IP69-sealed and hermetic solutions are available with a wide choice of materials and coatings to ensure their resistance to corrosion, while being lightweight and compact.
Underwater and high-pressure sealing
To withstand exposure for extended periods of time in liquids under high pressure, applications such as deep-submarine applications or pipeline-inspection equipment, and seismic-evaluation or drilling instruments in oil & gas, require waterproof connectors with special designs combining hermetic sealing with high-strength mechanical designs to guarantee safe and efficient operations.
Design engineers face special technical challenges for their marine and underwater applications such as autonomous and remotely operated underwater vehicles (ROV, AUV or UUV), which operate at depths where diving by humans is either impractical or dangerous.
Such demanding applications involved in immersion over long periods require ultra-sealed, watertight, cabled waterproof connectors that achieve an IP68 rating in both mated and unmated states.
Salt strongly increases water conductivity, so seawater and salt mist can act as an electrolyte, causing galvanic corrosion. Our IP68/IP69-sealed and hermetic solutions are available with a wide choice of materials and coatings to ensure their resistance to corrosion, while being lightweight and compact.
Underwater and high-pressure sealing
To withstand exposure for extended periods of time in liquids under high pressure, applications such as deep-submarine applications or pipeline-inspection equipment, and seismic-evaluation or drilling instruments in oil & gas, require waterproof connectors with special designs combining hermetic sealing with high-strength mechanical designs to guarantee safe and efficient operations.
Design engineers face special technical challenges for their marine and underwater applications such as autonomous and remotely operated underwater vehicles (ROV, AUV or UUV), which operate at depths where diving by humans is either impractical or dangerous.
Such demanding applications involved in immersion over long periods require ultra-sealed, watertight, cabled waterproof connectors that achieve an IP68 rating in both mated and unmated states.
Salt strongly increases water conductivity, so seawater and salt mist can act as an electrolyte, causing galvanic corrosion. Our IP68/IP69-sealed and hermetic solutions are available with a wide choice of materials and coatings to ensure their resistance to corrosion, while being lightweight and compact.
Ingress protection (IP)
Ingress protection (IP)
Ingress protection (IP)
The Ingress Protection (IP) classification system provides a method described in IEC 60529 for defining the sealing level of various electronic solutions and waterproof connector products. While the first number describes the level of protection from solid objects, the second one relates to protection from liquids. The digits indicate conformity with the conditions summarized in the table below.
The Ingress Protection (IP) classification system provides a method described in IEC 60529 for defining the sealing level of various electronic solutions and waterproof connector products. While the first number describes the level of protection from solid objects, the second one relates to protection from liquids. The digits indicate conformity with the conditions summarized in the table below.
The Ingress Protection (IP) classification system provides a method described in IEC 60529 for defining the sealing level of various electronic solutions and waterproof connector products. While the first number describes the level of protection from solid objects, the second one relates to protection from liquids. The digits indicate conformity with the conditions summarized in the table below.
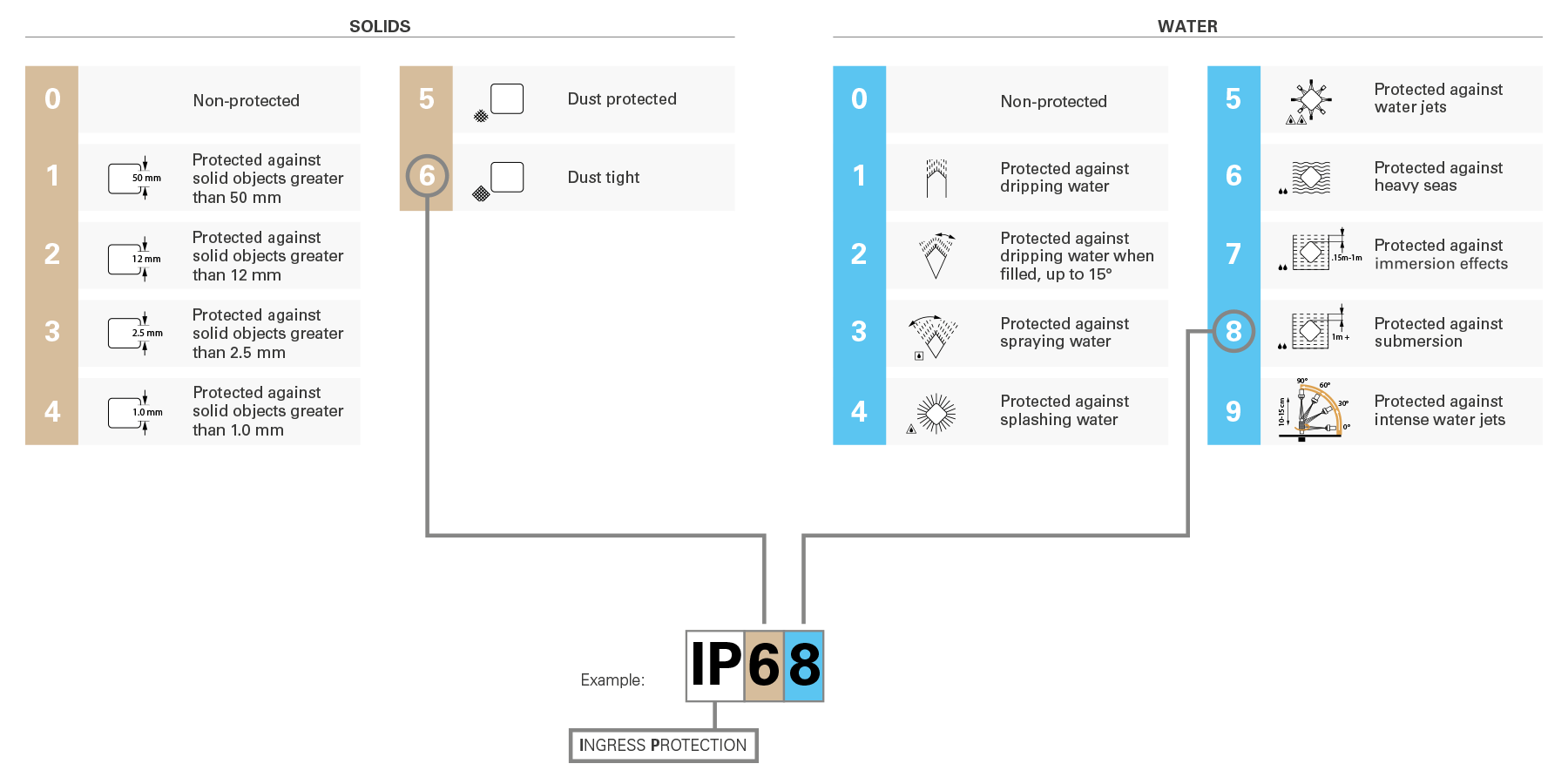
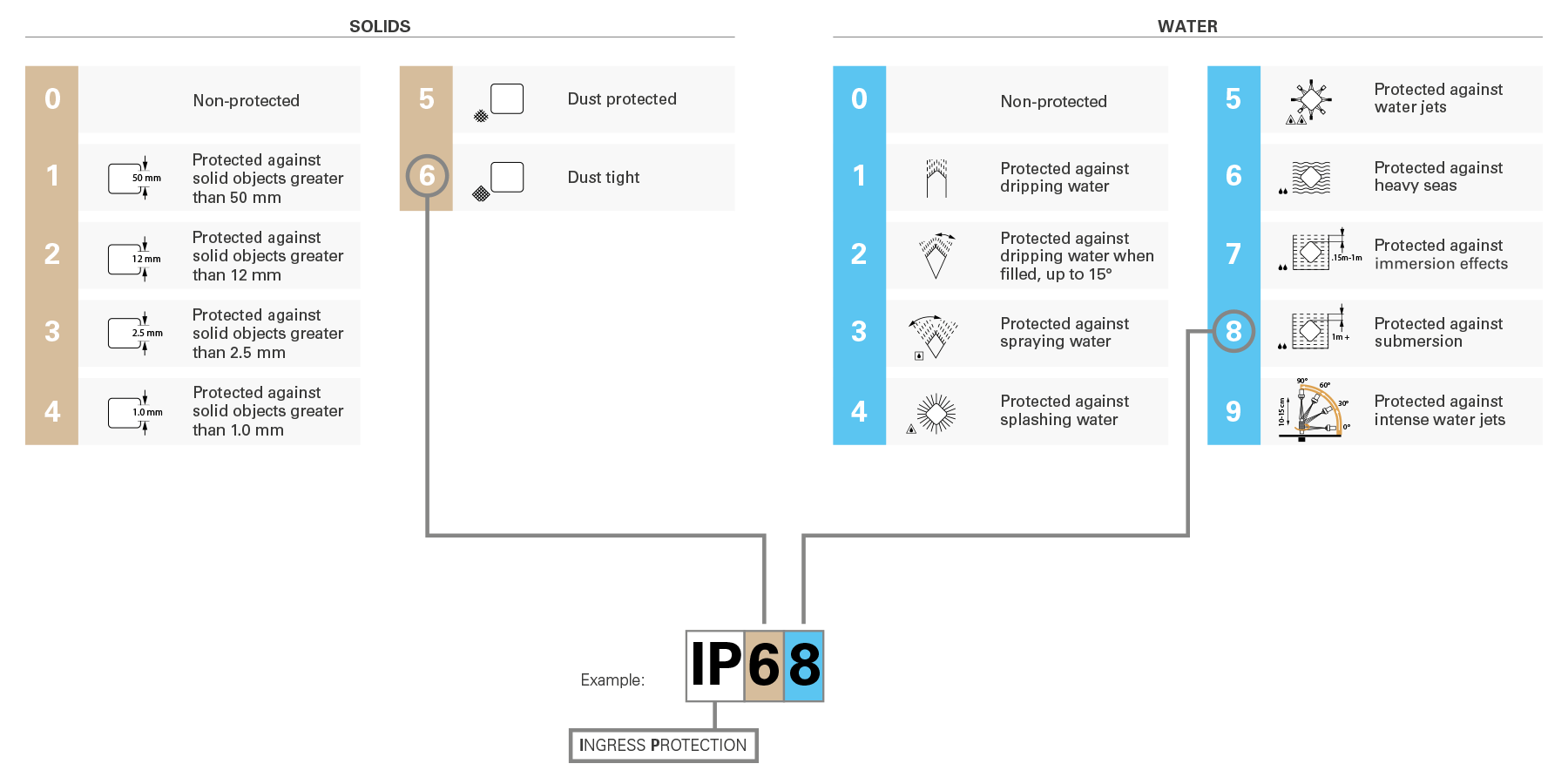
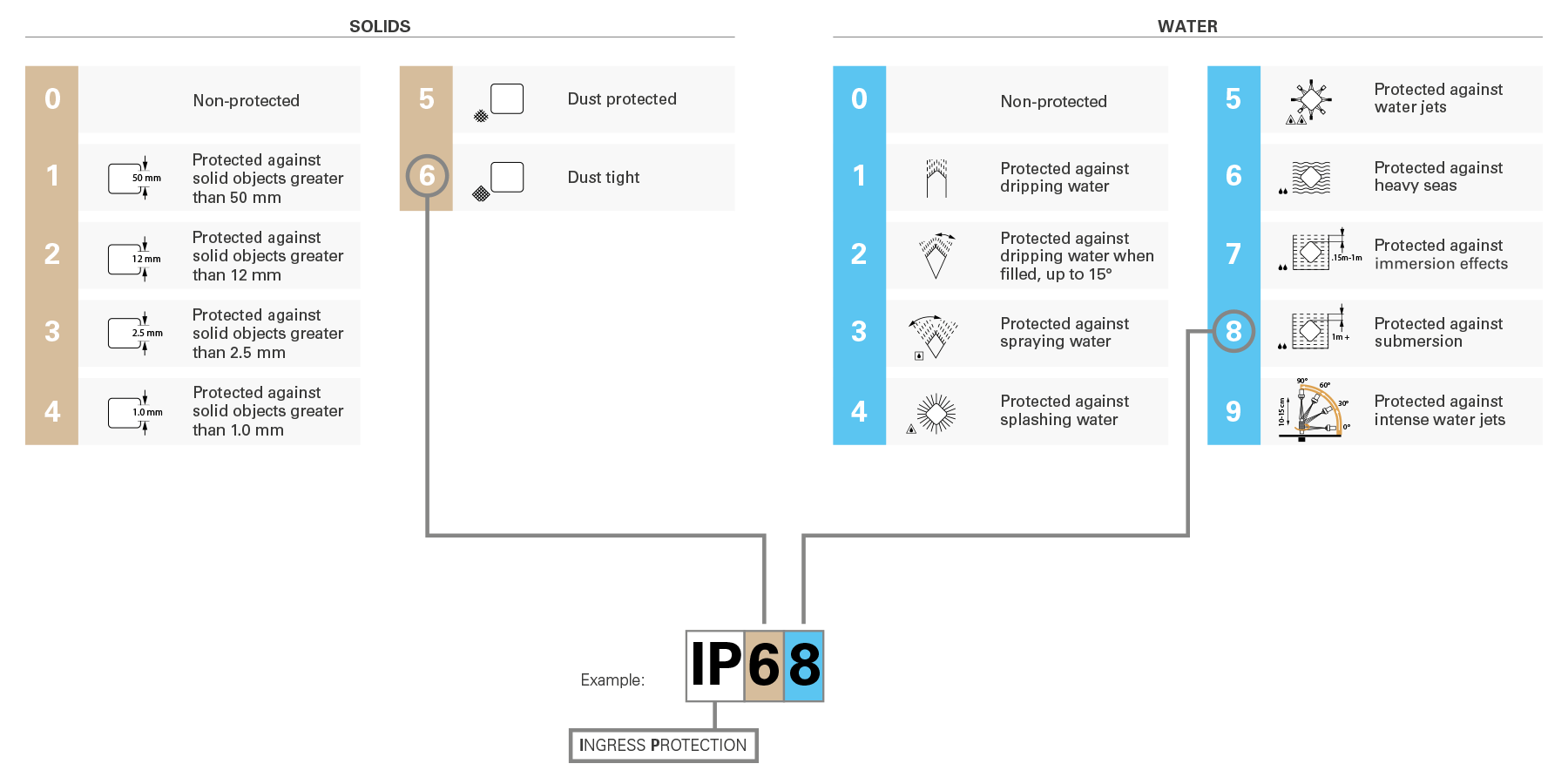
Examples of high-performance waterproof connector applications
Fischer Connectors’ waterproof connectivity solutions are trusted to endure harsh conditions in challenging environments.
Fischer Connectors’ waterproof connectivity solutions are trusted to endure harsh conditions in challenging environments.
Fischer Connectors’ waterproof connectivity solutions are trusted to endure harsh conditions in challenging environments.
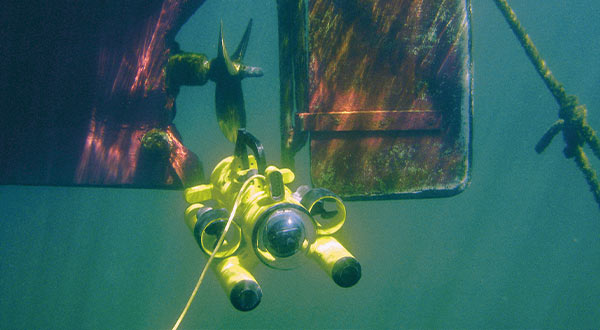
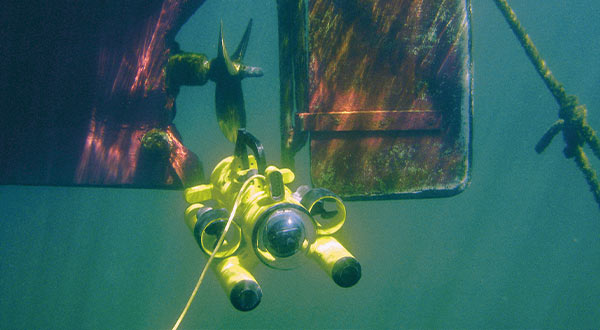
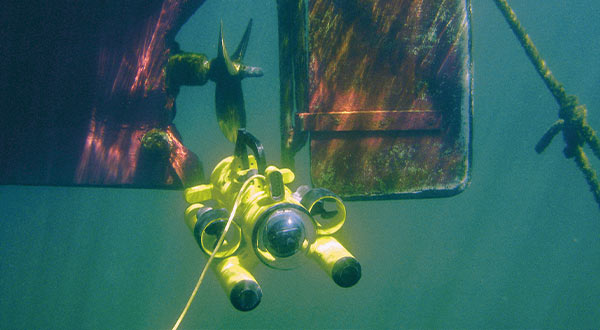
Unmanned underwater vehicles
Waterproof connectors are critical components for unmanned underwater vehicles (UUVs), as they provide the means for transmitting power, control signals, and data between the vehicle and its onboard systems or to external devices.
UUVs are often equipped with various sensors and other measurement instruments that collect and transmit data about the surrounding environment. Allowing for real-time monitoring and analysis, waterproof connectors enable the transmission of this data from the UUV to the surface or to other external devices.
Unmanned underwater vehicles
Waterproof connectors are critical components for unmanned underwater vehicles (UUVs), as they provide the means for transmitting power, control signals, and data between the vehicle and its onboard systems or to external devices.
UUVs are often equipped with various sensors and other measurement instruments that collect and transmit data about the surrounding environment. Allowing for real-time monitoring and analysis, waterproof connectors enable the transmission of this data from the UUV to the surface or to other external devices.
Unmanned underwater vehicles
Waterproof connectors are critical components for unmanned underwater vehicles (UUVs), as they provide the means for transmitting power, control signals, and data between the vehicle and its onboard systems or to external devices.
UUVs are often equipped with various sensors and other measurement instruments that collect and transmit data about the surrounding environment. Allowing for real-time monitoring and analysis, waterproof connectors enable the transmission of this data from the UUV to the surface or to other external devices.
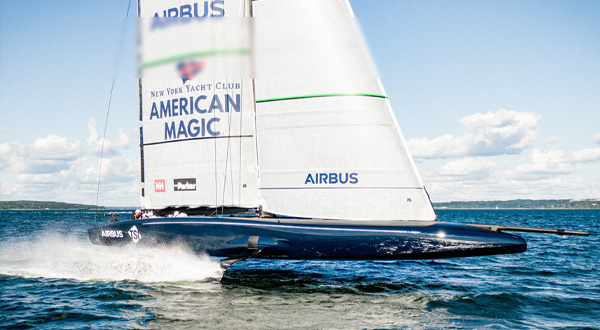
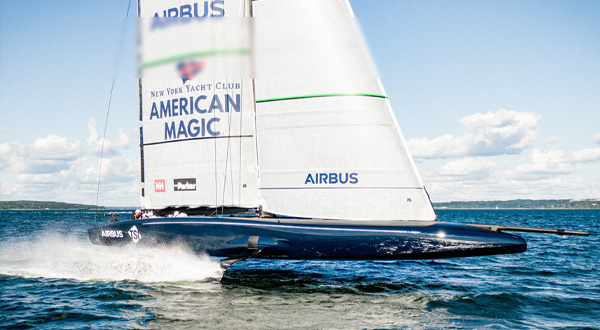
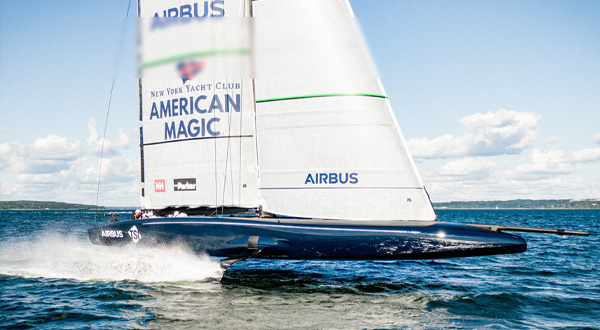
Yacht racing
Repair and maintenance costs can be high in yacht racing, and replacing damaged electrical components can be time-consuming and expensive. Waterproof connectors require minimal maintenance and have a longer lifespan, reducing the overall cost of ownership.
This discipline also requires peak performance from all electrical systems. Corrosion, short circuits, and other malfunctions that can affect the boat’s performance. Providing a better resistance, waterproof connectors ensure the functionality of the electrical systems.
Yacht racing
Repair and maintenance costs can be high in yacht racing, and replacing damaged electrical components can be time-consuming and expensive. Waterproof connectors require minimal maintenance and have a longer lifespan, reducing the overall cost of ownership.
This discipline also requires peak performance from all electrical systems. Corrosion, short circuits, and other malfunctions that can affect the boat’s performance. Providing a better resistance, waterproof connectors ensure the functionality of the electrical systems.
Yacht racing
Repair and maintenance costs can be high in yacht racing, and replacing damaged electrical components can be time-consuming and expensive. Waterproof connectors require minimal maintenance and have a longer lifespan, reducing the overall cost of ownership.
This discipline also requires peak performance from all electrical systems. Corrosion, short circuits, and other malfunctions that can affect the boat’s performance. Providing a better resistance, waterproof connectors ensure the functionality of the electrical systems.
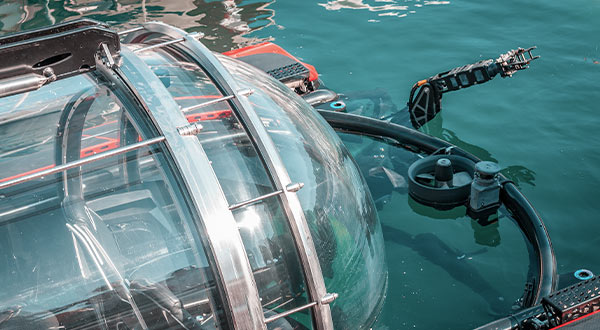
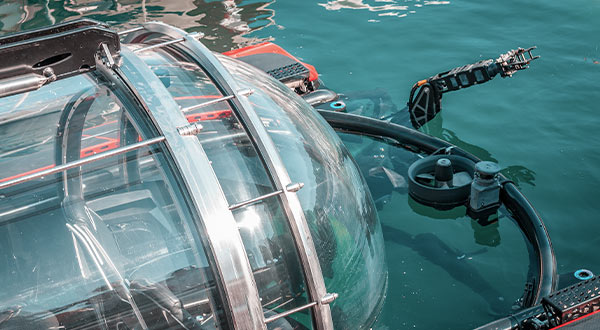
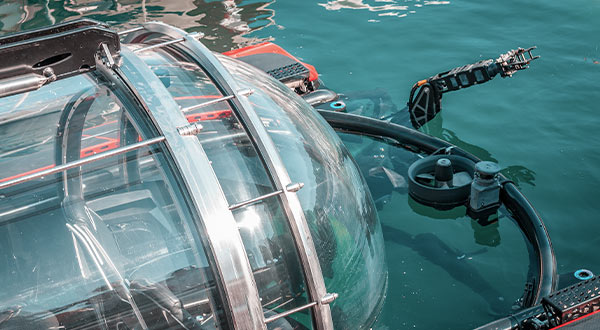
Underwater scientific instrumentation
Underwater scientific instruments often need to withstand harsh conditions, including extreme pressure, saltwater corrosion, and varying water temperatures. As such, it is important to use waterproof connectors that can withstand these conditions and protect the sensitive equipment inside.
In addition, waterproof connectors help to minimize the risk of electrical shorts and failures, which can compromise data collection and analysis.
Underwater scientific instrumentation
Underwater scientific instruments often need to withstand harsh conditions, including extreme pressure, saltwater corrosion, and varying water temperatures. As such, it is important to use waterproof connectors that can withstand these conditions and protect the sensitive equipment inside.
In addition, waterproof connectors help to minimize the risk of electrical shorts and failures, which can compromise data collection and analysis.
Underwater scientific instrumentation
Underwater scientific instruments often need to withstand harsh conditions, including extreme pressure, saltwater corrosion, and varying water temperatures. As such, it is important to use waterproof connectors that can withstand these conditions and protect the sensitive equipment inside.
In addition, waterproof connectors help to minimize the risk of electrical shorts and failures, which can compromise data collection and analysis.
Environmental connector sealing explained
Sealing techniques for environmental protection
The most robust waterproof connectors have barriers in multiple places, protecting against dirt and water from various angles and intensities. Fischer Connectors’ products designed for rugged conditions, unlike standard commercial or consumer-grade connectors, have clearly independent sealing functions designed to control the waterproof connector’s performance for every requirement. Several advanced sealing functions can be found on high-quality environmentally sealed products:
Sealing techniques for environmental protection
The most robust waterproof connectors have barriers in multiple places, protecting against dirt and water from various angles and intensities. Fischer Connectors’ products designed for rugged conditions, unlike standard commercial or consumer-grade connectors, have clearly independent sealing functions designed to control the waterproof connector’s performance for every requirement. Several advanced sealing functions can be found on high-quality environmentally sealed products:
Sealing techniques for environmental protection
The most robust waterproof connectors have barriers in multiple places, protecting against dirt and water from various angles and intensities. Fischer Connectors’ products designed for rugged conditions, unlike standard commercial or consumer-grade connectors, have clearly independent sealing functions designed to control the waterproof connector’s performance for every requirement. Several advanced sealing functions can be found on high-quality environmentally sealed products:
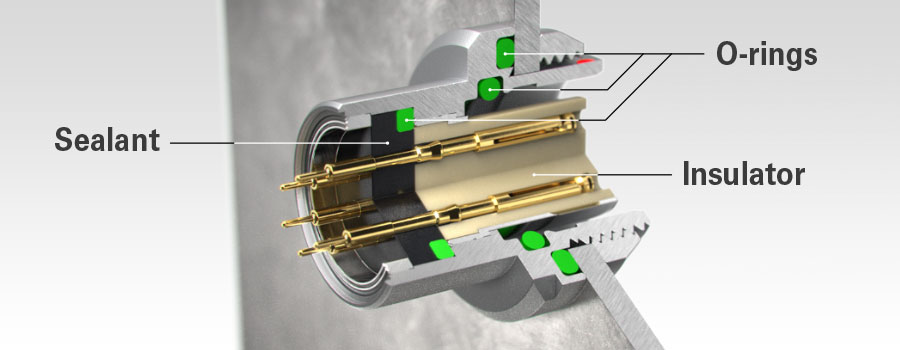
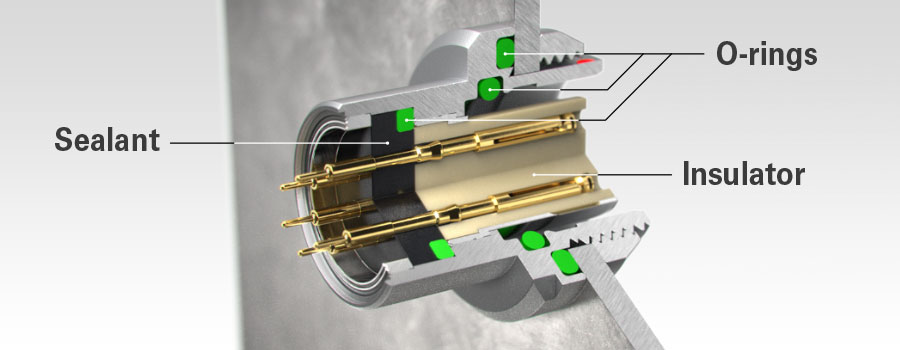
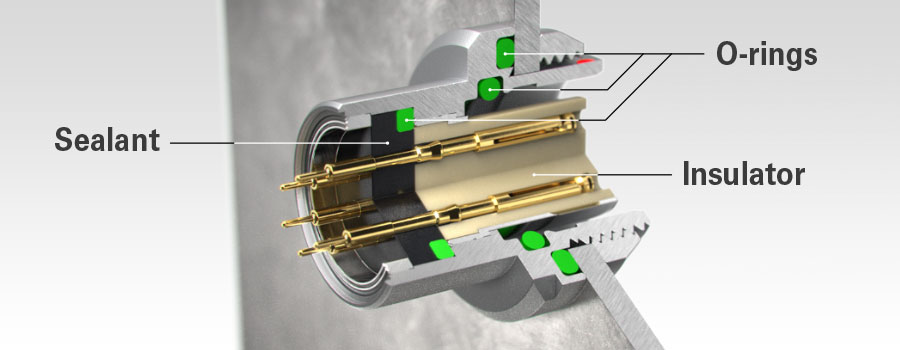
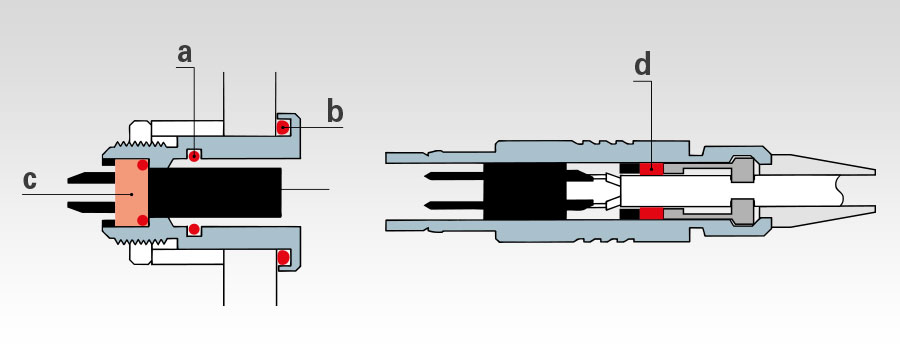
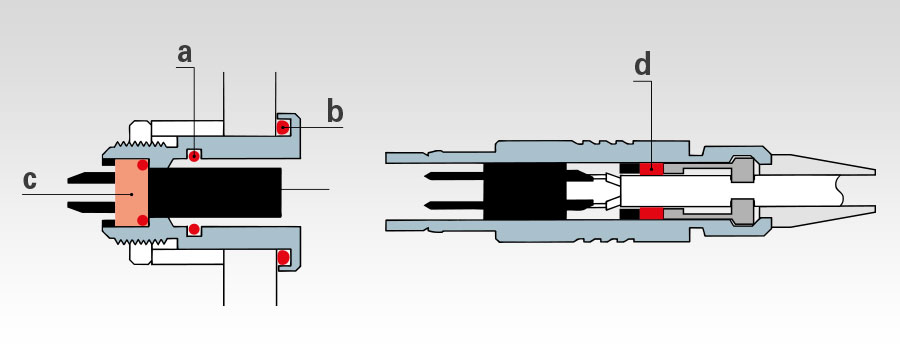
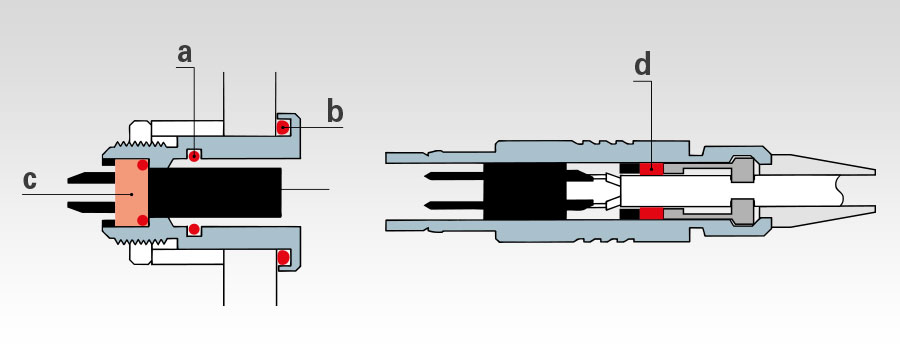
Interface seal
By definition, this seal protects the waterproof connector interface, i.e. the junction between two connectors. It prevents ingress of water or harmful particles into the connection area where male and female contacts mate. This seal’s function is to ensure long-term product reliability, especially if the waterproof connector is frequently mated and unmated.
Because the interface seal works dynamically when mating, and can be exposed to the environment, you should select the quality of the seal according to operating temperature, environment and fluids.
Panel seal
This sealing element joins the waterproof connector housing with the panel or equipment housing. The seal works in a static way; in most applications, its exposure to the environment is very limited due to the recessed O-ring position. Most standard, sealed Fischer Connectors products come with a panel seal.
Sealing of block
Normally an open connector should be protected against environmental influences when disconnected, by using an adequate protective cap. However, in some cases the waterproof connector must remain sealed even without protective accessories. In this case, the inner contact block of the receptacle must also be sealed to prevent dust or water ingress into the equipment. High-quality sealing compounds are used for factory sealing of the block. Although this is a standard process on environmentally sealed products, it is incompatible with designs in which contacts are put into place by the customer (crimp contacts). In such cases, the use of protective caps is mandatory.
Interface seal
By definition, this seal protects the waterproof connector interface, i.e. the junction between two connectors. It prevents ingress of water or harmful particles into the connection area where male and female contacts mate. This seal’s function is to ensure long-term product reliability, especially if the waterproof connector is frequently mated and unmated.
Because the interface seal works dynamically when mating, and can be exposed to the environment, you should select the quality of the seal according to operating temperature, environment and fluids.
Panel seal
This sealing element joins the waterproof connector housing with the panel or equipment housing. The seal works in a static way; in most applications, its exposure to the environment is very limited due to the recessed O-ring position. Most standard, sealed Fischer Connectors products come with a panel seal.
Sealing of block
Normally an open connector should be protected against environmental influences when disconnected, by using an adequate protective cap. However, in some cases the waterproof connector must remain sealed even without protective accessories. In this case, the inner contact block of the receptacle must also be sealed to prevent dust or water ingress into the equipment. High-quality sealing compounds are used for factory sealing of the block. Although this is a standard process on environmentally sealed products, it is incompatible with designs in which contacts are put into place by the customer (crimp contacts). In such cases, the use of protective caps is mandatory.
Interface seal
By definition, this seal protects the waterproof connector interface, i.e. the junction between two connectors. It prevents ingress of water or harmful particles into the connection area where male and female contacts mate. This seal’s function is to ensure long-term product reliability, especially if the waterproof connector is frequently mated and unmated.
Because the interface seal works dynamically when mating, and can be exposed to the environment, you should select the quality of the seal according to operating temperature, environment and fluids.
Panel seal
This sealing element joins the waterproof connector housing with the panel or equipment housing. The seal works in a static way; in most applications, its exposure to the environment is very limited due to the recessed O-ring position. Most standard, sealed Fischer Connectors products come with a panel seal.
Sealing of block
Normally an open connector should be protected against environmental influences when disconnected, by using an adequate protective cap. However, in some cases the waterproof connector must remain sealed even without protective accessories. In this case, the inner contact block of the receptacle must also be sealed to prevent dust or water ingress into the equipment. High-quality sealing compounds are used for factory sealing of the block. Although this is a standard process on environmentally sealed products, it is incompatible with designs in which contacts are put into place by the customer (crimp contacts). In such cases, the use of protective caps is mandatory.
Cable seal
This grommet-type seal is designed to protect your connection solution by preventing the ingress of liquids into the waterproof connector along the cable. Cable material and quality strongly affect the reliability of this seal; careful selection is essential to properly match the diameter of the seal to the diameter of the cable. Separate, environmentally sealed clamp sets are available for all common Fischer Connectors plugs.
Sealing materials
It is important to understand the quality of the sealing materials your manufacturer selects. Fischer Connectors selects materials based on solutions that have proven high reliability in many difficult operating conditions. Standard sealing materials are:
- Viton® is a fluoropolymer often designated FKM. Its low permeation and excellent broad chemical resistance are interesting for many applications. Fischer Connectors uses Viton® as its first choice for most receptacle seals.
- EPDM (ethylene propylene rubber) is another elastomer characterized by a wide range of applications. Commonly used as weather seals on vehicles, it combines good water resistance with low glass transition temperature. EPDM is the preferred choice for interface O-rings in waterproof connectors designed to be mated and unmated at low temperatures.
Fischer Connectors also offers a wide range of custom solutions for applications where special sealing requirements are essential.
Cable seal
This grommet-type seal is designed to protect your connection solution by preventing the ingress of liquids into the waterproof connector along the cable. Cable material and quality strongly affect the reliability of this seal; careful selection is essential to properly match the diameter of the seal to the diameter of the cable. Separate, environmentally sealed clamp sets are available for all common Fischer Connectors plugs.
Sealing materials
It is important to understand the quality of the sealing materials your manufacturer selects. Fischer Connectors selects materials based on solutions that have proven high reliability in many difficult operating conditions. Standard sealing materials are:
- Viton® is a fluoropolymer often designated FKM. Its low permeation and excellent broad chemical resistance are interesting for many applications. Fischer Connectors uses Viton® as its first choice for most receptacle seals.
- EPDM (ethylene propylene rubber) is another elastomer characterized by a wide range of applications. Commonly used as weather seals on vehicles, it combines good water resistance with low glass transition temperature. EPDM is the preferred choice for interface O-rings in waterproof connectors designed to be mated and unmated at low temperatures.
Fischer Connectors also offers a wide range of custom solutions for applications where special sealing requirements are essential.
Cable seal
This grommet-type seal is designed to protect your connection solution by preventing the ingress of liquids into the waterproof connector along the cable. Cable material and quality strongly affect the reliability of this seal; careful selection is essential to properly match the diameter of the seal to the diameter of the cable. Separate, environmentally sealed clamp sets are available for all common Fischer Connectors plugs.
Sealing materials
It is important to understand the quality of the sealing materials your manufacturer selects. Fischer Connectors selects materials based on solutions that have proven high reliability in many difficult operating conditions. Standard sealing materials are:
- Viton® is a fluoropolymer often designated FKM. Its low permeation and excellent broad chemical resistance are interesting for many applications. Fischer Connectors uses Viton® as its first choice for most receptacle seals.
- EPDM (ethylene propylene rubber) is another elastomer characterized by a wide range of applications. Commonly used as weather seals on vehicles, it combines good water resistance with low glass transition temperature. EPDM is the preferred choice for interface O-rings in waterproof connectors designed to be mated and unmated at low temperatures.
Fischer Connectors also offers a wide range of custom solutions for applications where special sealing requirements are essential.
Sealing standards
Sealing standards
Sealing standards
The protection level offered by a typical envelope (IP rating) is described in IEC 60529. When waterproof connectors will be used in harsh operating environments, check the manufacturer’s IP rating for sealing to dust and water at various depths and operating time frames. Make sure you understand the end-use environment for your waterproof connectors, and then compare that scenario with the details behind the manufacturer’s IP rating.
Most of the IP designations have specific conditions, but the IP68 rating may be defined differently by each manufacturer. When looking for a waterproof connector with an IP68 sealing rating, inquire exactly how the manufacturer’s IP68 rating is measured. Being submerged at 2 meters for 24 hours has a different impact on the waterproof connector than at 120 meters for 24 hours, but both situations can be defined as an IP68 rating.
The protection level offered by a typical envelope (IP rating) is described in IEC 60529. When waterproof connectors will be used in harsh operating environments, check the manufacturer’s IP rating for sealing to dust and water at various depths and operating time frames. Make sure you understand the end-use environment for your waterproof connectors, and then compare that scenario with the details behind the manufacturer’s IP rating.
Most of the IP designations have specific conditions, but the IP68 rating may be defined differently by each manufacturer. When looking for a waterproof connector with an IP68 sealing rating, inquire exactly how the manufacturer’s IP68 rating is measured. Being submerged at 2 meters for 24 hours has a different impact on the waterproof connector than at 120 meters for 24 hours, but both situations can be defined as an IP68 rating.
The protection level offered by a typical envelope (IP rating) is described in IEC 60529. When waterproof connectors will be used in harsh operating environments, check the manufacturer’s IP rating for sealing to dust and water at various depths and operating time frames. Make sure you understand the end-use environment for your waterproof connectors, and then compare that scenario with the details behind the manufacturer’s IP rating.
Most of the IP designations have specific conditions, but the IP68 rating may be defined differently by each manufacturer. When looking for a waterproof connector with an IP68 sealing rating, inquire exactly how the manufacturer’s IP68 rating is measured. Being submerged at 2 meters for 24 hours has a different impact on the waterproof connector than at 120 meters for 24 hours, but both situations can be defined as an IP68 rating.
Environmental tests performed during the design and qualification of Fischer Connectors’ environmentally sealed products are standardized to IP68 at a depth of 2 m and duration of 24 hours.
IP69K is an additional sealing level defined to protect an envelope from intense water jets for a short duration (typically for high-pressure cleaning). IP69K is a definition from the German DIN 40050-9.
Environmental tests performed during the design and qualification of Fischer Connectors’ environmentally sealed products are standardized to IP68 at a depth of 2 m and duration of 24 hours.
IP69K is an additional sealing level defined to protect an envelope from intense water jets for a short duration (typically for high-pressure cleaning). IP69K is a definition from the German DIN 40050-9.
Environmental tests performed during the design and qualification of Fischer Connectors’ environmentally sealed products are standardized to IP68 at a depth of 2 m and duration of 24 hours.
IP69K is an additional sealing level defined to protect an envelope from intense water jets for a short duration (typically for high-pressure cleaning). IP69K is a definition from the German DIN 40050-9.