Medical connectors
Our high-performance connectors are designed for demanding medical settings, including diagnostic, imaging, surgical, therapeutic, and dental healthcare. They can be fully customized or purchased off-the-shelf.
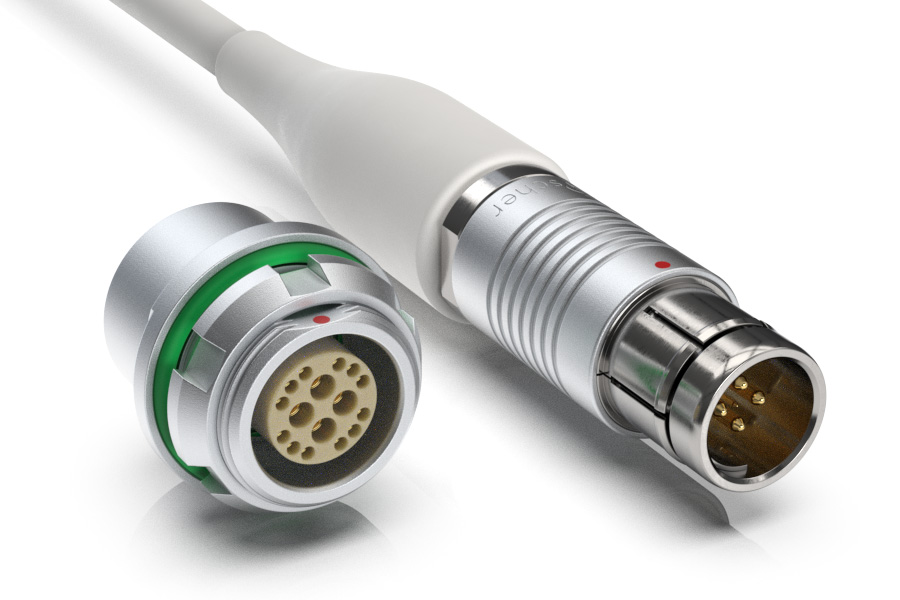
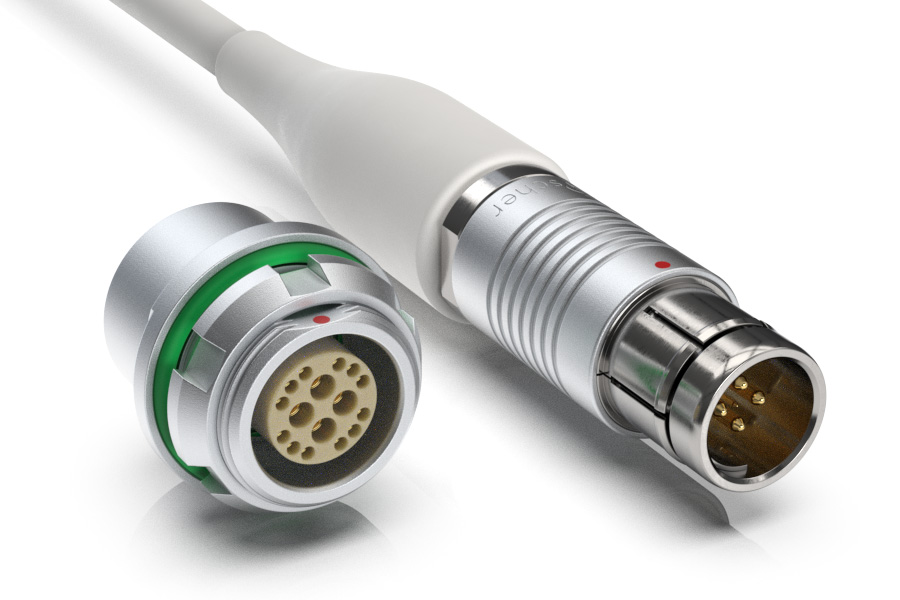
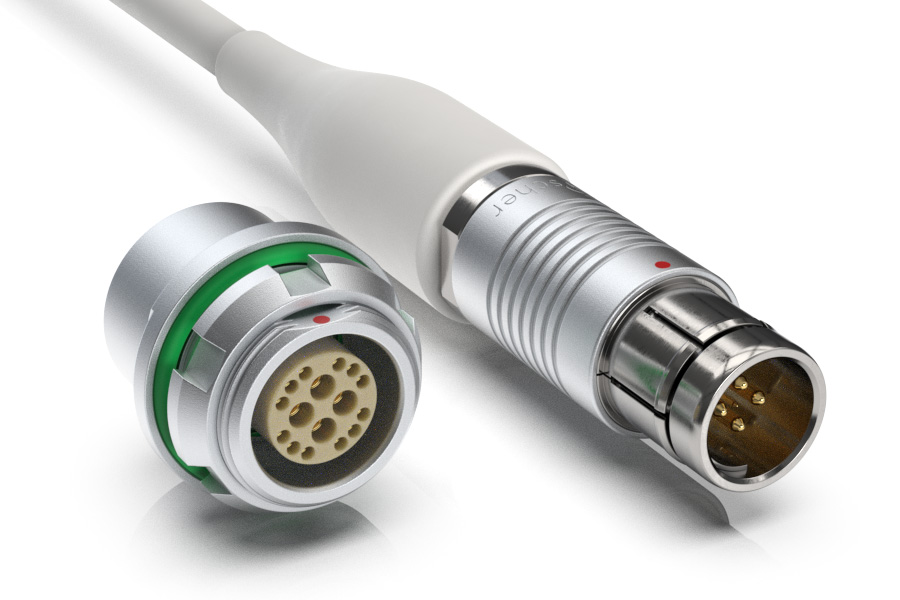
Our wide range of circular connectors – including miniature, sterilizable, reusable, hybrid, disposable and silicone-coated options – meet the strictest quality and reliability requirements in medical device manufacturing.
Our wide range of circular connectors – including miniature, sterilizable, reusable, hybrid, disposable and silicone-coated options – meet the strictest quality and reliability requirements in medical device manufacturing.
Our wide range of circular connectors – including miniature, sterilizable, reusable, hybrid, disposable and silicone-coated options – meet the strictest quality and reliability requirements in medical device manufacturing.
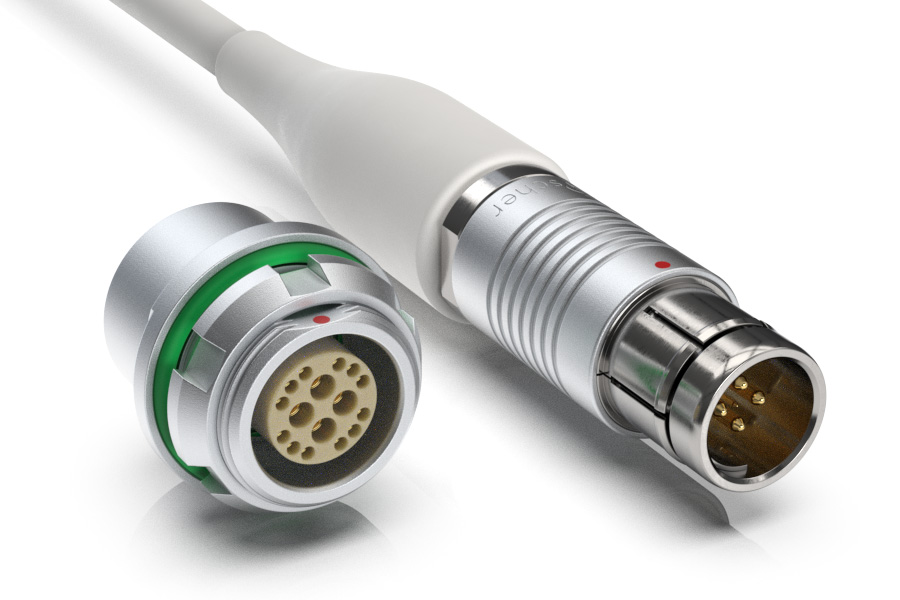
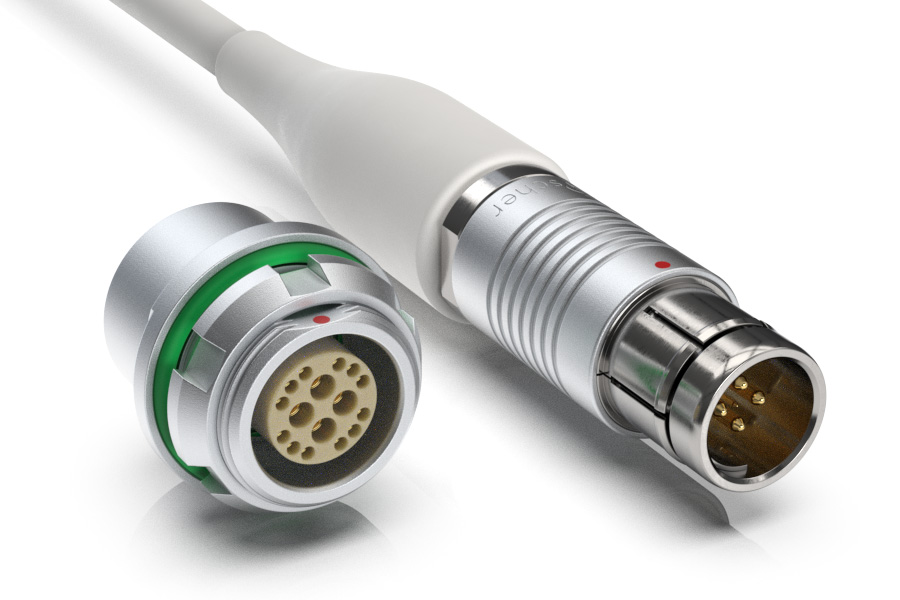
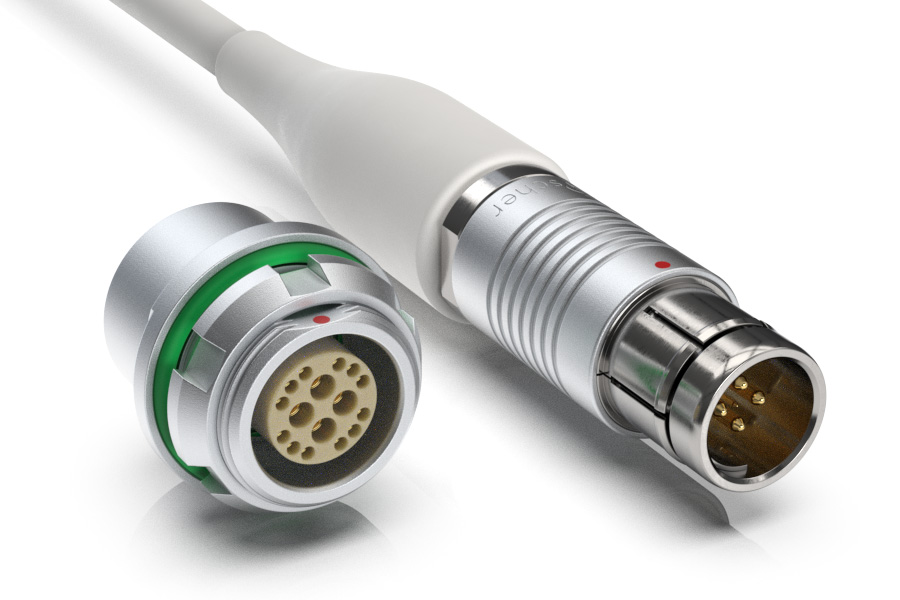
Our wide range of circular connectors – including miniature, sterilizable, reusable, hybrid, disposable and silicone-coated options – meet the strictest quality and reliability requirements in medical device manufacturing.
Our wide range of circular connectors – including miniature, sterilizable, reusable, hybrid, disposable and silicone-coated options – meet the strictest quality and reliability requirements in medical device manufacturing.
Our wide range of circular connectors – including miniature, sterilizable, reusable, hybrid, disposable and silicone-coated options – meet the strictest quality and reliability requirements in medical device manufacturing.
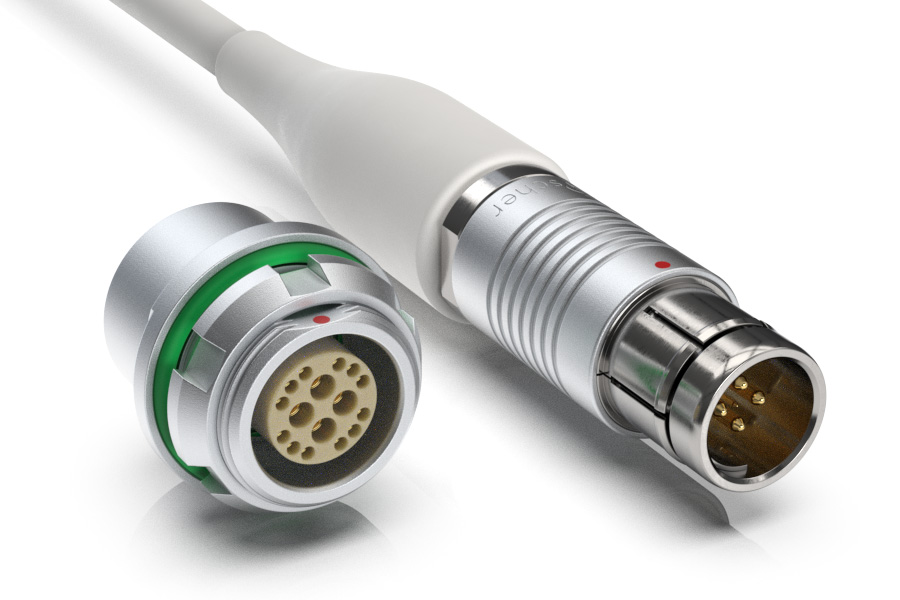
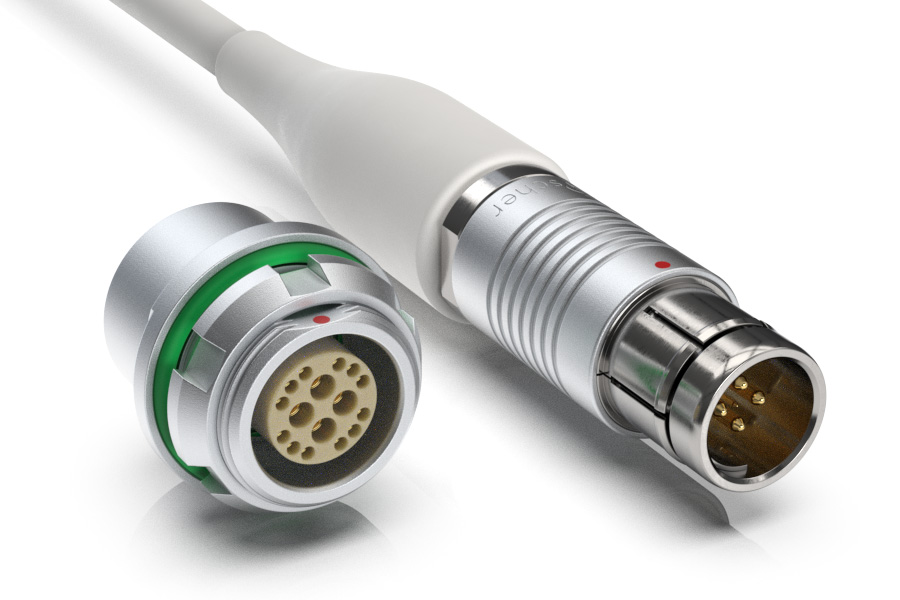
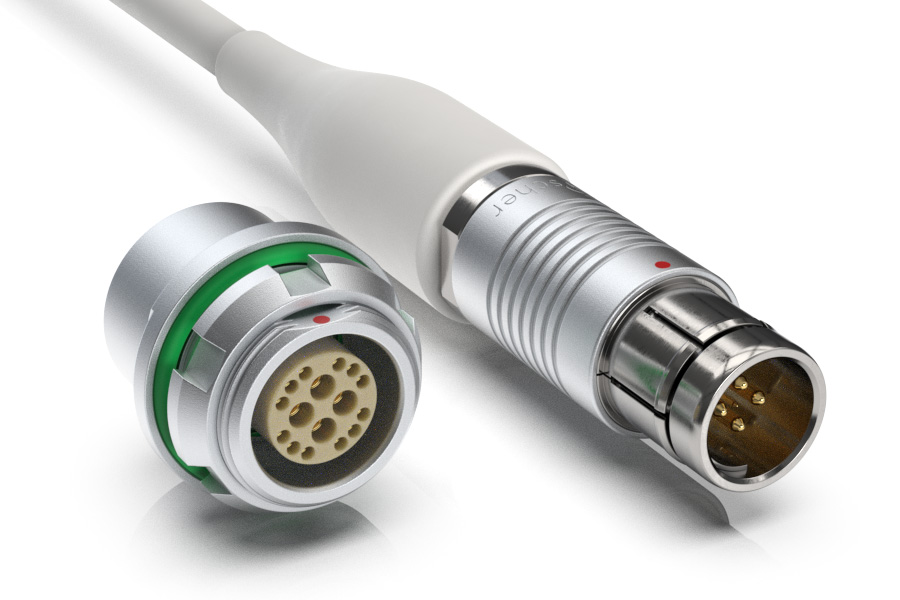
Our wide range of circular connectors – including miniature, sterilizable, reusable, hybrid, disposable and silicone-coated options – meet the strictest quality and reliability requirements in medical device manufacturing.
Our wide range of circular connectors – including miniature, sterilizable, reusable, hybrid, disposable and silicone-coated options – meet the strictest quality and reliability requirements in medical device manufacturing.
Our wide range of circular connectors – including miniature, sterilizable, reusable, hybrid, disposable and silicone-coated options – meet the strictest quality and reliability requirements in medical device manufacturing.
Sales request
Get STEP files and product information
Our medical connector solutions
Fischer Connectors is known for its reliable, durable medical device solutions. Our connectors help create smaller, lighter devices for less invasive patient interactions. They include hybrid configurations that combine data, power, and fluids in a single cable/connector.
Our organization is committed to ensuring the safety of medical patients by developing and providing products, services, and solutions that meet the highest industry standards. We are ISO 13485:2016 certified for quality management and offer products and solutions compliant with IEC 60601-1 for patient and operator protection (MOPP/MOOP).
Fischer Connectors is known for its reliable, durable medical device solutions. Our connectors help create smaller, lighter devices for less invasive patient interactions. They include hybrid configurations that combine data, power, and fluids in a single cable/connector.
Our organization is committed to ensuring the safety of medical patients by developing and providing products, services, and solutions that meet the highest industry standards. We are ISO 13485:2016 certified for quality management and offer products and solutions compliant with IEC 60601-1 for patient and operator protection (MOPP/MOOP).
Fischer Connectors is known for its reliable, durable medical device solutions. Our connectors help create smaller, lighter devices for less invasive patient interactions. They include hybrid configurations that combine data, power, and fluids in a single cable/connector.
Our organization is committed to ensuring the safety of medical patients by developing and providing products, services, and solutions that meet the highest industry standards. We are ISO 13485:2016 certified for quality management and offer products and solutions compliant with IEC 60601-1 for patient and operator protection (MOPP/MOOP).
Key features
- Sterilization proof: Autocave (500 cycles minimum), Cidex, EtO, Gamma radiation, Steris® or Sterrad®
- IP68 sealing, resistance to heat and chemicals
- Robust design with mechanical endurance of 10’000 mating cycles minimum
- Highly configurable with a wide choice of high-performance materials (brass, stainless steel, plastic, PEEK) and customization capabilities
- Miniature and lightweight options
- Friction-free and flexible silicone overmolding
- Ergonomic and easy to handle and clean
- Combination of power and data, gas or fluids
- Optimized signal integrity
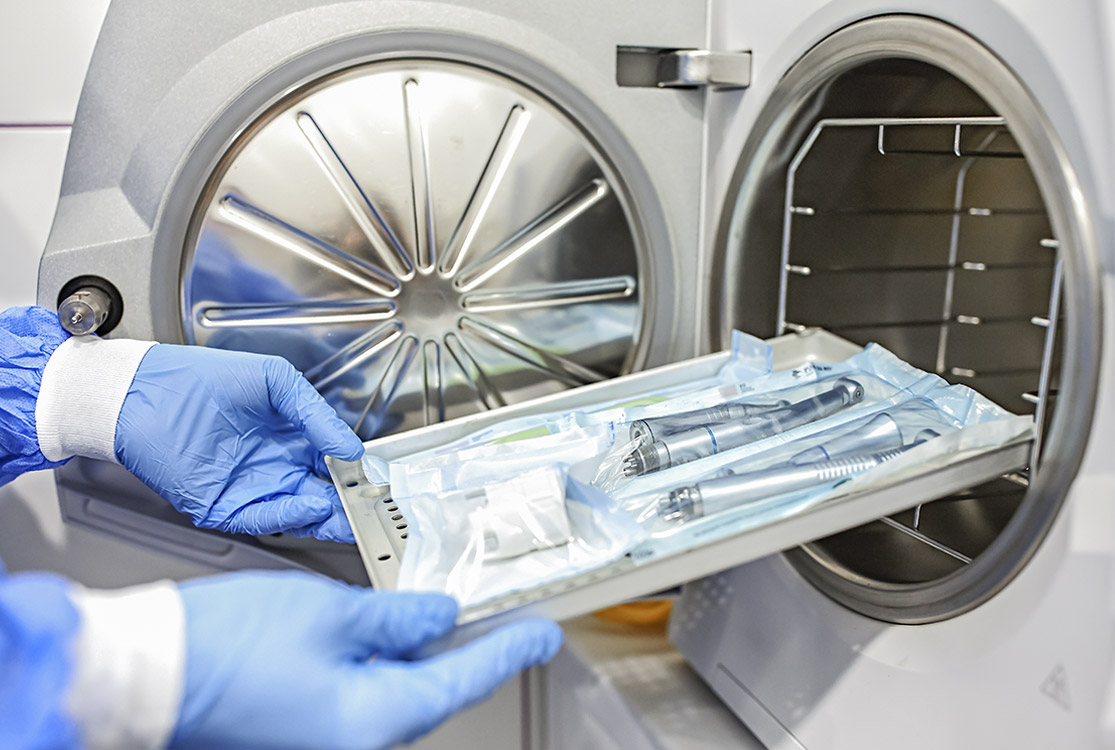
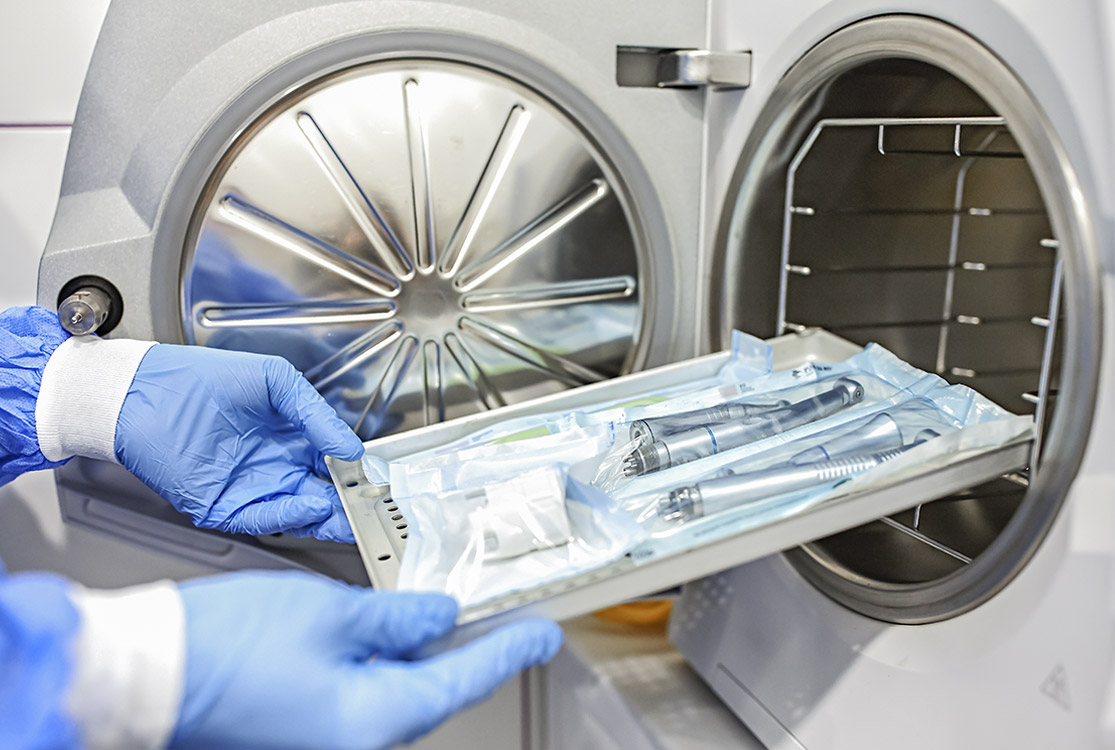
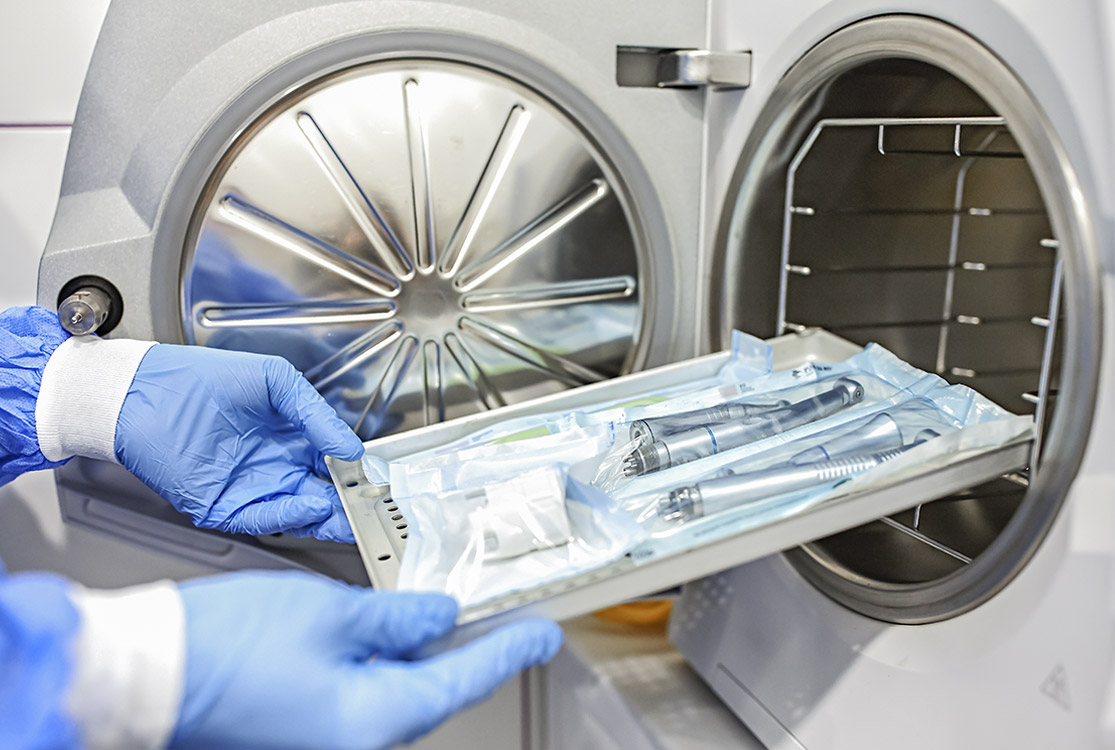
Our product range
Our product range
Our product range
Need other features?
Our custom connector capabilities will help you meet your needs.
Learn more about medical connectors
Medtech designers face strict safety requirements for both patients and operators. Devices undergo extensive FDA and European trials, making risk reduction a top priority for designers.
Manufacturers need to ensure that medical devices are low-risk, reliable, modern-looking, and provide a positive patient experience, all while incorporating more technology and functionality in a smaller space.
Medical connectors and cable assemblies play a crucial role in delivering power to hand tools, handheld diagnostic equipment, and transmitting signals to mobile consoles and surgical systems.
Selecting the right medical connector and cable assembly solution is crucial for creating small, safe, stylish, and functional devices at a competitive price, while minimizing risks for both patients and operators.
Medtech designers face strict safety requirements for both patients and operators. Devices undergo extensive FDA and European trials, making risk reduction a top priority for designers.
Manufacturers need to ensure that medical devices are low-risk, reliable, modern-looking, and provide a positive patient experience, all while incorporating more technology and functionality in a smaller space.
Medical connectors and cable assemblies play a crucial role in delivering power to hand tools, handheld diagnostic equipment, and transmitting signals to mobile consoles and surgical systems.
Selecting the right medical connector and cable assembly solution is crucial for creating small, safe, stylish, and functional devices at a competitive price, while minimizing risks for both patients and operators.
Medtech designers face strict safety requirements for both patients and operators. Devices undergo extensive FDA and European trials, making risk reduction a top priority for designers.
Manufacturers need to ensure that medical devices are low-risk, reliable, modern-looking, and provide a positive patient experience, all while incorporating more technology and functionality in a smaller space.
Medical connectors and cable assemblies play a crucial role in delivering power to hand tools, handheld diagnostic equipment, and transmitting signals to mobile consoles and surgical systems.
Selecting the right medical connector and cable assembly solution is crucial for creating small, safe, stylish, and functional devices at a competitive price, while minimizing risks for both patients and operators.
Critical considerations for material choice, required sealing level and mating mechanism:
- How many mating cycles is the medical connector expected to last ?
- Who will operate, clean and sterilize the device: untrained patient or a trained medical professional ?
- What kind of conditions the device will need to endure ?
- Which sterilization method will be applied will be ?
It’s important to shield medical connectors from electromagnetic interference (EMI/RFI) to ensure reliable data transmission, as many everyday electronics emit EM energy.
Critical considerations for material choice, required sealing level and mating mechanism:
- How many mating cycles is the medical connector expected to last ?
- Who will operate, clean and sterilize the device: untrained patient or a trained medical professional ?
- What kind of conditions the device will need to endure ?
- Which sterilization method will be applied will be ?
It’s important to shield medical connectors from electromagnetic interference (EMI/RFI) to ensure reliable data transmission, as many everyday electronics emit EM energy.
Critical considerations for material choice, required sealing level and mating mechanism:
- How many mating cycles is the medical connector expected to last ?
- Who will operate, clean and sterilize the device: untrained patient or a trained medical professional ?
- What kind of conditions the device will need to endure ?
- Which sterilization method will be applied will be ?
It’s important to shield medical connectors from electromagnetic interference (EMI/RFI) to ensure reliable data transmission, as many everyday electronics emit EM energy.
Connector Size | Take a close look at who will be managing the connection. A patient who is sick and self-managing will have different needs than a caregiver or medical professional. Make sure your connector is small enough to help keep design in line, but large enough for anyone to get a good grip on it. In addition, keep an eye on the profile of the connector. The lower, the better when it comes to wearables. |
Connections for Patient Mobility | If you are looking at mobility, look at how and how much the patient will be moving. Lots of mobility will mean a different set of design considerations than if a person is bedridden. New options for the most mobile patients include connectors with concentric rings that allow movement of the cable, making it less likely to be damaged over time. |
Connector Torque | Many connectors are purposely designed so that it is hard to connect or disconnect. Make sure that the connector is easy enough to connect and disconnect, but difficult to accidently disconnect. |
Shape & Locking Types | We admit to bias here, but we think circular push-pull connectors are perfect for wearables, with no little tabs to break off, rectangles to challenge your spatial awareness, or USB-type hassles when you can’t find the right way to place the connector into the receptacle no matter how many times you turn it over. Circular connectors also have quick-release/no lock solutions or if you need it to stay in place in high vibrations, look for a screw lock. |
Cable Management | Wearables and devices that move around a lot require pre-planning for cable length and how the cables need to move with the person or the device. Think about sewing cables into clothing to minimize a patent’s ability to damage or tangle them. Make sure there is enough (but not too much) cable. You may want to consider offering different lengths of cable. Robotic devices and exoskeletons with embedded sensors also need protected cable systems. |
EMI Shielding | The more technology in the area, the more you need EMI shielding to protect the system from the noise. But you can’t skip EMI protections just because a product will have in-home use. Medical devices are critical, and you can’t predict electrical interference on that alone. |
Color | The more connectors, the more color-coding you want to consider. Minimize the number of colors needed with multi-use connectors for signal and power or air and signal. Look at materials that can be ordered in different colors, or rings that match connector or cable colors. |
Connector Size | Take a close look at who will be managing the connection. A patient who is sick and self-managing will have different needs than a caregiver or medical professional. Make sure your connector is small enough to help keep design in line, but large enough for anyone to get a good grip on it. In addition, keep an eye on the profile of the connector. The lower, the better when it comes to wearables. |
Connections for Patient Mobility | If you are looking at mobility, look at how and how much the patient will be moving. Lots of mobility will mean a different set of design considerations than if a person is bedridden. New options for the most mobile patients include connectors with concentric rings that allow movement of the cable, making it less likely to be damaged over time. |
Connector Torque | Many connectors are purposely designed so that it is hard to connect or disconnect. Make sure that the connector is easy enough to connect and disconnect, but difficult to accidently disconnect. |
Shape & Locking Types | We admit to bias here, but we think circular push-pull connectors are perfect for wearables, with no little tabs to break off, rectangles to challenge your spatial awareness, or USB-type hassles when you can’t find the right way to place the connector into the receptacle no matter how many times you turn it over. Circular connectors also have quick-release/no lock solutions or if you need it to stay in place in high vibrations, look for a screw lock. |
Cable Management | Wearables and devices that move around a lot require pre-planning for cable length and how the cables need to move with the person or the device. Think about sewing cables into clothing to minimize a patent’s ability to damage or tangle them. Make sure there is enough (but not too much) cable. You may want to consider offering different lengths of cable. Robotic devices and exoskeletons with embedded sensors also need protected cable systems. |
EMI Shielding | The more technology in the area, the more you need EMI shielding to protect the system from the noise. But you can’t skip EMI protections just because a product will have in-home use. Medical devices are critical, and you can’t predict electrical interference on that alone. |
Color | The more connectors, the more color-coding you want to consider. Minimize the number of colors needed with multi-use connectors for signal and power or air and signal. Look at materials that can be ordered in different colors, or rings that match connector or cable colors. |
Connector Size | Take a close look at who will be managing the connection. A patient who is sick and self-managing will have different needs than a caregiver or medical professional. Make sure your connector is small enough to help keep design in line, but large enough for anyone to get a good grip on it. In addition, keep an eye on the profile of the connector. The lower, the better when it comes to wearables. |
Connections for Patient Mobility | If you are looking at mobility, look at how and how much the patient will be moving. Lots of mobility will mean a different set of design considerations than if a person is bedridden. New options for the most mobile patients include connectors with concentric rings that allow movement of the cable, making it less likely to be damaged over time. |
Connector Torque | Many connectors are purposely designed so that it is hard to connect or disconnect. Make sure that the connector is easy enough to connect and disconnect, but difficult to accidently disconnect. |
Shape & Locking Types | We admit to bias here, but we think circular push-pull connectors are perfect for wearables, with no little tabs to break off, rectangles to challenge your spatial awareness, or USB-type hassles when you can’t find the right way to place the connector into the receptacle no matter how many times you turn it over. Circular connectors also have quick-release/no lock solutions or if you need it to stay in place in high vibrations, look for a screw lock. |
Cable Management | Wearables and devices that move around a lot require pre-planning for cable length and how the cables need to move with the person or the device. Think about sewing cables into clothing to minimize a patent’s ability to damage or tangle them. Make sure there is enough (but not too much) cable. You may want to consider offering different lengths of cable. Robotic devices and exoskeletons with embedded sensors also need protected cable systems. |
EMI Shielding | The more technology in the area, the more you need EMI shielding to protect the system from the noise. But you can’t skip EMI protections just because a product will have in-home use. Medical devices are critical, and you can’t predict electrical interference on that alone. |
Color | The more connectors, the more color-coding you want to consider. Minimize the number of colors needed with multi-use connectors for signal and power or air and signal. Look at materials that can be ordered in different colors, or rings that match connector or cable colors. |
Safety
- ESD (electrostatic discharge) protection
- MOPP (Means of Patient Protection), MOOP (Means of Operator Protection) and compliance with test finger standard
- Air clearance and creepage distances
- Insulation barriers and insulated contacts
Signal integrity optimization
- Highs-speed multiprotocol data transfer
- Minimized noise and signal distortion
- Controlled cable assembly process for impedance matching
- Minimized near-end / far-end crosstalk (NEXT / FEXT)
Durability
- 500 sterilization cycles proven
- Resistant to sterilization and chemicals (autoclave, Cidex, EtO, Gamma radiation, Steris® or Sterrad®)
- Resistant to high-pressure steam (hydrogen peroxide vapor, Sterrad®)
- Thermal insulation
- Available with silicone overmolding
Custom designs
- Brass, stainless steel, plastic, PEEK
- Custom color coding and locking mechanisms
- Miniature and lightweight
- Ergonomic and easy to handle
- Hybrid connectivity – fluidic / optical / electrical
- Robust design with double shielding
Our spectrum of medical connector applications
Fischer Connectors is proud to be recognized as an essential partner for medical device manufacturing, serving leading organizations and suppliers. These solutions help protect and save lives across various applications :
Fischer Connectors is proud to be recognized as an essential partner for medical device manufacturing, serving leading organizations and suppliers. These solutions help protect and save lives across various applications :
Fischer Connectors is proud to be recognized as an essential partner for medical device manufacturing, serving leading organizations and suppliers. These solutions help protect and save lives across various applications :



Diagnostic & Imaging
Fischer Connectors provides dependable, high-speed connectivity solutions for accurate imaging and diagnostics, e.g., endoscopy, laparoscopy, electroencephalography (EEG), MRI and CT scanners or medical ultrasound.
For safe diagnostic procedures with reusable endoscopes, the connectivity solution must be hermetically sealed to protect electronics from cleaning, disinfection, and reprocessing. It’s recommended to use durable medical connectors with metal shells and cables with silicone overmolding to withstand between 250 and 1,000 cycles as per reprocessing guidelines.
Fischer Connectors offers a wide range of sizes, configurations and coding options for medical connectors which withstand extreme sterilization processes and feature more than 5,000 mating cycles.
Diagnostic & Imaging
Fischer Connectors provides dependable, high-speed connectivity solutions for accurate imaging and diagnostics, e.g., endoscopy, laparoscopy, electroencephalography (EEG), MRI and CT scanners or medical ultrasound.
For safe diagnostic procedures with reusable endoscopes, the connectivity solution must be hermetically sealed to protect electronics from cleaning, disinfection, and reprocessing. It’s recommended to use durable medical connectors with metal shells and cables with silicone overmolding to withstand between 250 and 1,000 cycles as per reprocessing guidelines.
Fischer Connectors offers a wide range of sizes, configurations and coding options for medical connectors which withstand extreme sterilization processes and feature more than 5,000 mating cycles.
Diagnostic & Imaging
Fischer Connectors provides dependable, high-speed connectivity solutions for accurate imaging and diagnostics, e.g., endoscopy, laparoscopy, electroencephalography (EEG), MRI and CT scanners or medical ultrasound.
For safe diagnostic procedures with reusable endoscopes, the connectivity solution must be hermetically sealed to protect electronics from cleaning, disinfection, and reprocessing. It’s recommended to use durable medical connectors with metal shells and cables with silicone overmolding to withstand between 250 and 1,000 cycles as per reprocessing guidelines.
Fischer Connectors offers a wide range of sizes, configurations and coding options for medical connectors which withstand extreme sterilization processes and feature more than 5,000 mating cycles.
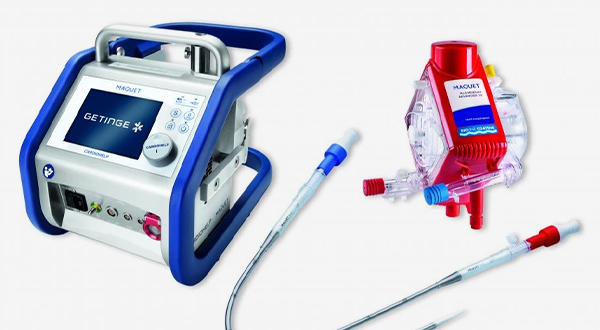
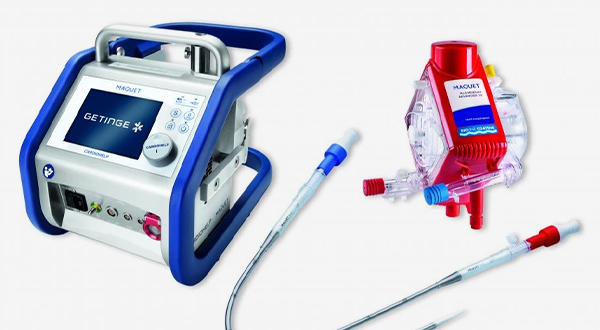
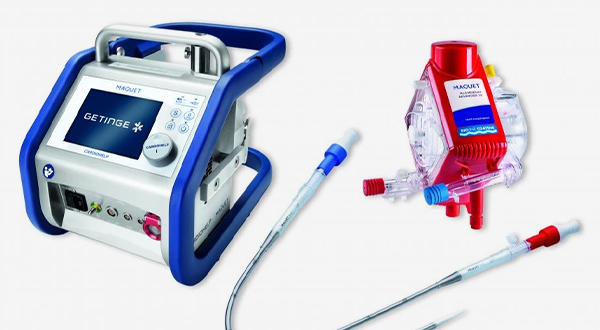
Monitoring
Our medical connectors feature reliable and straightforward connectivity technology for vital patient information, critical care and rescue operations, e.g., Getinge’s Cardiohelp. This mobile heart-lung support system is easy to use and quick to set up in a wide range of indications in cardiac surgery, cardiology, intensive care and emergency medicine.
The manufacturer selected Fischer Core connectors for their durability, high-quality mating, reliable signal transmission, and user-friendliness. The medical connectors also had to be easy to clean and robust against harsh cleaning agents.
Monitoring
Our medical connectors feature reliable and straightforward connectivity technology for vital patient information, critical care and rescue operations, e.g., Getinge’s Cardiohelp. This mobile heart-lung support system is easy to use and quick to set up in a wide range of indications in cardiac surgery, cardiology, intensive care and emergency medicine.
The manufacturer selected Fischer Core connectors for their durability, high-quality mating, reliable signal transmission, and user-friendliness. The medical connectors also had to be easy to clean and robust against harsh cleaning agents.
Monitoring
Our medical connectors feature reliable and straightforward connectivity technology for vital patient information, critical care and rescue operations, e.g., Getinge’s Cardiohelp. This mobile heart-lung support system is easy to use and quick to set up in a wide range of indications in cardiac surgery, cardiology, intensive care and emergency medicine.
The manufacturer selected Fischer Core connectors for their durability, high-quality mating, reliable signal transmission, and user-friendliness. The medical connectors also had to be easy to clean and robust against harsh cleaning agents.
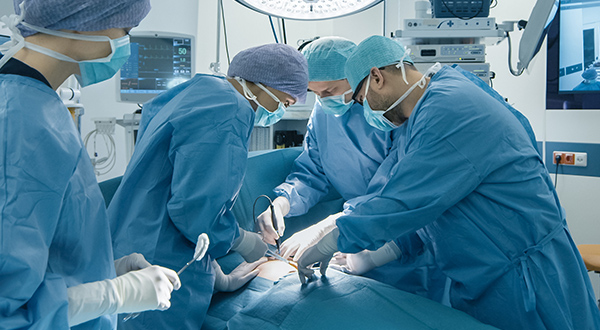
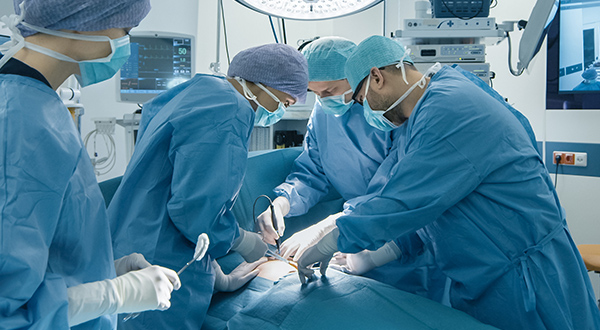
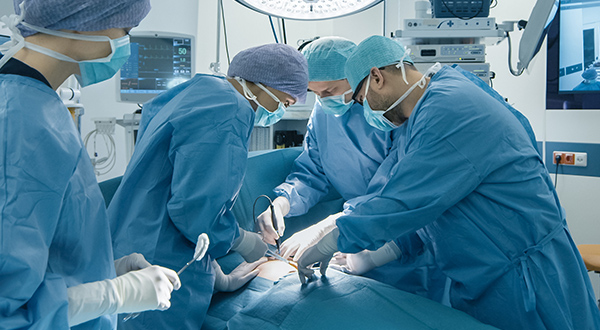
Interventional & Surgical
At Fischer Connectors, we provide secure and durable connectivity solutions for high-precision devices in robot-assisted and dental surgery, shaver systems, power consoles, and powered instrument drivers for surgical procedures.
Our medical connectors are designed to withstand the demands of surgical applications, with features such as hermetic sealing, high mating cycles, and resistance to harsh cleaning agents or sterilization procedures, while ensuring signal integrity for reliable data transmission. The flexibility in design ensures seamless integration into medical devices for improved performance.
Interventional & Surgical
At Fischer Connectors, we provide secure and durable connectivity solutions for high-precision devices in robot-assisted and dental surgery, shaver systems, power consoles, and powered instrument drivers for surgical procedures.
Our medical connectors are designed to withstand the demands of surgical applications, with features such as hermetic sealing, high mating cycles, and resistance to harsh cleaning agents or sterilization procedures, while ensuring signal integrity for reliable data transmission. The flexibility in design ensures seamless integration into medical devices for improved performance.
Interventional & Surgical
At Fischer Connectors, we provide secure and durable connectivity solutions for high-precision devices in robot-assisted and dental surgery, shaver systems, power consoles, and powered instrument drivers for surgical procedures.
Our medical connectors are designed to withstand the demands of surgical applications, with features such as hermetic sealing, high mating cycles, and resistance to harsh cleaning agents or sterilization procedures, while ensuring signal integrity for reliable data transmission. The flexibility in design ensures seamless integration into medical devices for improved performance.
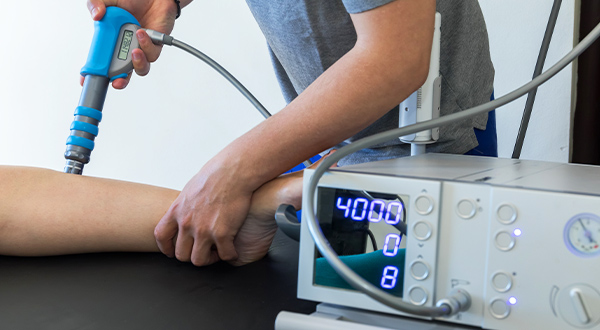
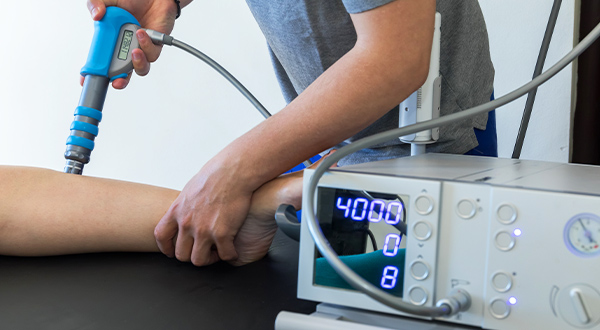
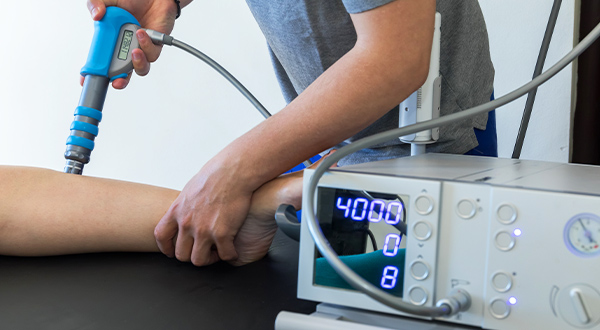
Therapeutic
Our connectivity solutions are widely used in therapeutic devices, particularly in shock-wave medical applications, where our durable and reliable connectors are essential for withstanding demanding conditions including exposure to shock and vibration.
They provide reliable signal transmission and ensure secure mating, ensuring that the shock wave machine functions optimally without any disruptions or malfunctions.
Therapeutic
Our connectivity solutions are widely used in therapeutic devices, particularly in shock-wave medical applications, where our durable and reliable connectors are essential for withstanding demanding conditions including exposure to shock and vibration.
They provide reliable signal transmission and ensure secure mating, ensuring that the shock wave machine functions optimally without any disruptions or malfunctions.
Therapeutic
Our connectivity solutions are widely used in therapeutic devices, particularly in shock-wave medical applications, where our durable and reliable connectors are essential for withstanding demanding conditions including exposure to shock and vibration.
They provide reliable signal transmission and ensure secure mating, ensuring that the shock wave machine functions optimally without any disruptions or malfunctions.
At Fischer Connectors, we offer fully integrated connectivity solutions to facilitate the implementation of the Internet of Medical Things (IoMT).
At Fischer Connectors, we offer fully integrated connectivity solutions to facilitate the implementation of the Internet of Medical Things (IoMT).
At Fischer Connectors, we offer fully integrated connectivity solutions to facilitate the implementation of the Internet of Medical Things (IoMT).
Miniaturization in medical connectors
The trend toward miniaturization in medtech is driving the need for small, rugged medical connectors capable of handling signal and power transmission in compact devices. These innovations are crucial for mobile and patient-worn devices, as well as new sensor technologies for wireless reporting.
Designing small medical connectors requires careful consideration of material, pin density, and electrical capacity to ensure optimal performance and safety. Proper testing and custom cable solutions may be necessary to achieve the best fit and functionality in these miniaturized medical devices.
The trend toward miniaturization in medtech is driving the need for small, rugged medical connectors capable of handling signal and power transmission in compact devices. These innovations are crucial for mobile and patient-worn devices, as well as new sensor technologies for wireless reporting.
Designing small medical connectors requires careful consideration of material, pin density, and electrical capacity to ensure optimal performance and safety. Proper testing and custom cable solutions may be necessary to achieve the best fit and functionality in these miniaturized medical devices.
The trend toward miniaturization in medtech is driving the need for small, rugged medical connectors capable of handling signal and power transmission in compact devices. These innovations are crucial for mobile and patient-worn devices, as well as new sensor technologies for wireless reporting.
Designing small medical connectors requires careful consideration of material, pin density, and electrical capacity to ensure optimal performance and safety. Proper testing and custom cable solutions may be necessary to achieve the best fit and functionality in these miniaturized medical devices.
Device type | Connector Consideration | Cable Consideration |
Surgical hand tools |
|
Must be sterilizable. Consider high-heat silicone with a low friction coating. |
Dental hand tools |
|
Lightweight, but small and strong enough to handle the power required |
Handheld diagnostic devices |
|
May be sterilizable. Color-code overmolding for ease of use Lightweight cable with high EMI protection |
Patient Care and Monitoring (home or office care) |
|
Color-coded cable and overmolds when multiple connectors are in use |
Surgical robotics |
|
High degree of flexibility |
Portable medical consoles |
|
Effective high-speed communication via required protocol |
Imaging devices |
|
High speed video data cables often required |
Wearables |
|
Light, flexible cables. May consider a ribbon cable for a lower profile |
Device type | Connector Consideration | Cable Consideration |
Surgical hand tools |
|
Must be sterilizable. Consider high-heat silicone with a low friction coating. |
Dental hand tools |
|
Lightweight, but small and strong enough to handle the power required |
Handheld diagnostic devices |
|
May be sterilizable. Color-code overmolding for ease of use Lightweight cable with high EMI protection |
Patient Care and Monitoring (home or office care) |
|
Color-coded cable and overmolds when multiple connectors are in use |
Surgical robotics |
|
High degree of flexibility |
Portable medical consoles |
|
Effective high-speed communication via required protocol |
Imaging devices |
|
High speed video data cables often required |
Wearables |
|
Light, flexible cables. May consider a ribbon cable for a lower profile |
Device type | Connector Consideration | Cable Consideration |
Surgical hand tools |
|
Must be sterilizable. Consider high-heat silicone with a low friction coating. |
Dental hand tools |
|
Lightweight, but small and strong enough to handle the power required |
Handheld diagnostic devices |
|
May be sterilizable. Color-code overmolding for ease of use Lightweight cable with high EMI protection |
Patient Care and Monitoring (home or office care) |
|
Color-coded cable and overmolds when multiple connectors are in use |
Surgical robotics |
|
High degree of flexibility |
Portable medical consoles |
|
Effective high-speed communication via required protocol |
Imaging devices |
|
High speed video data cables often required |
Wearables |
|
Light, flexible cables. May consider a ribbon cable for a lower profile |