Hermetic connectors
Hermetically sealed connectors are used in many applications where gas leakage into or out of equipment must be avoided.
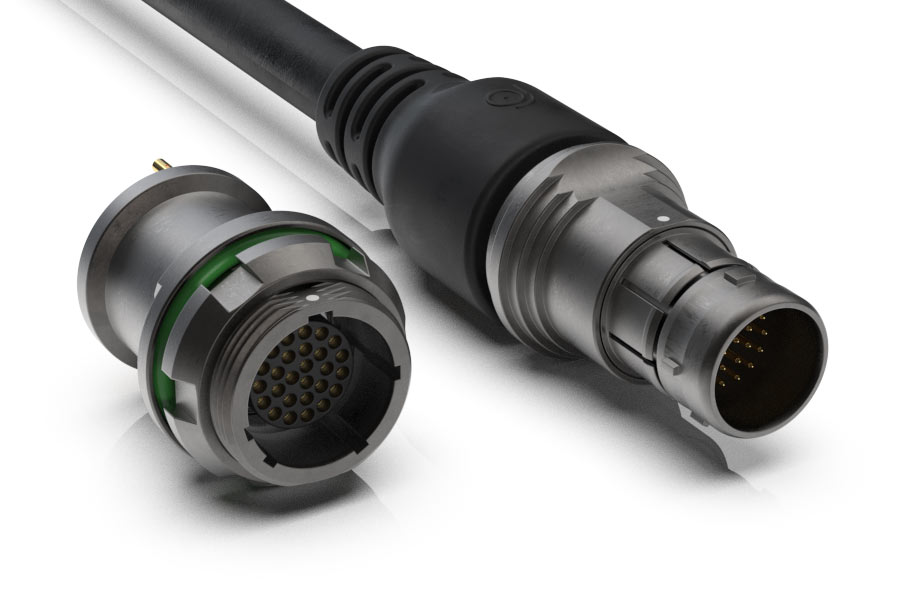
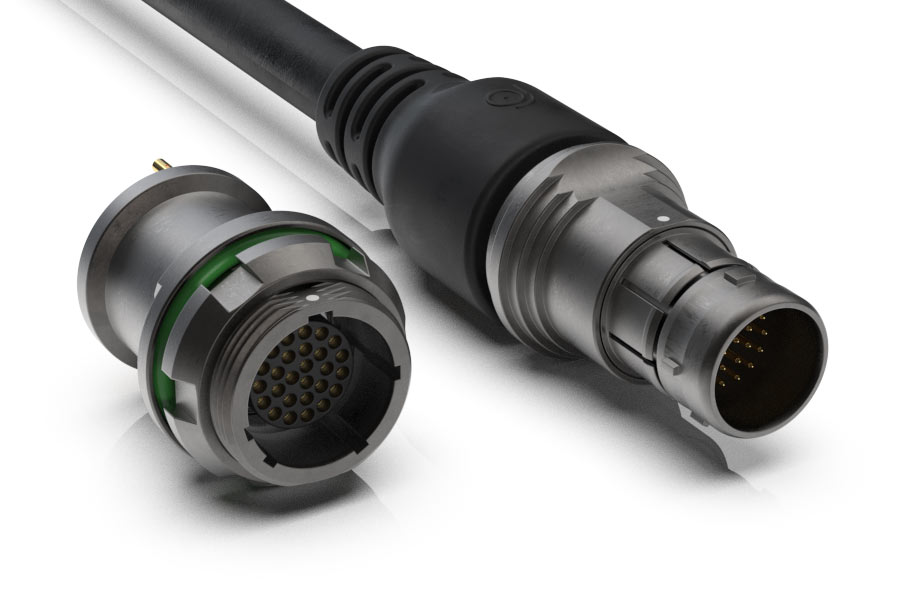
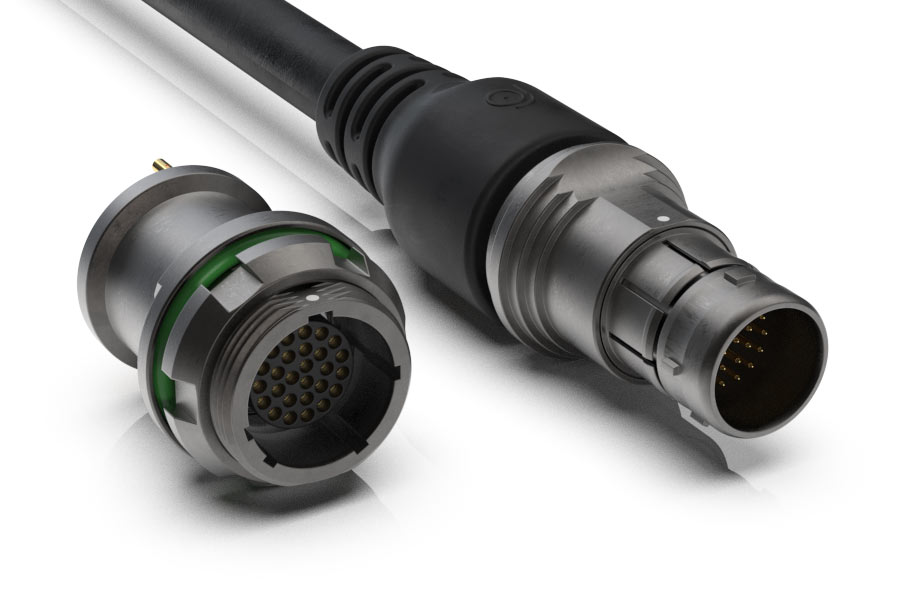
Sealing is a very complex science itself, as it involves many physical aspects including mechanical design, materials science, surface science, and fluid behavior.
Hermeticity is one of the toughest challenges that design engineers face when specifying the connectors needed for their device, since their applications require the tightest sealing that will not just keep dust and water out but will provide a barrier to gases down to the molecular level, i.e., gas tightness.
Sealing is a very complex science itself, as it involves many physical aspects including mechanical design, materials science, surface science, and fluid behavior.
Hermeticity is one of the toughest challenges that design engineers face when specifying the connectors needed for their device, since their applications require the tightest sealing that will not just keep dust and water out but will provide a barrier to gases down to the molecular level, i.e., gas tightness.
Sealing is a very complex science itself, as it involves many physical aspects including mechanical design, materials science, surface science, and fluid behavior.
Hermeticity is one of the toughest challenges that design engineers face when specifying the connectors needed for their device, since their applications require the tightest sealing that will not just keep dust and water out but will provide a barrier to gases down to the molecular level, i.e., gas tightness.
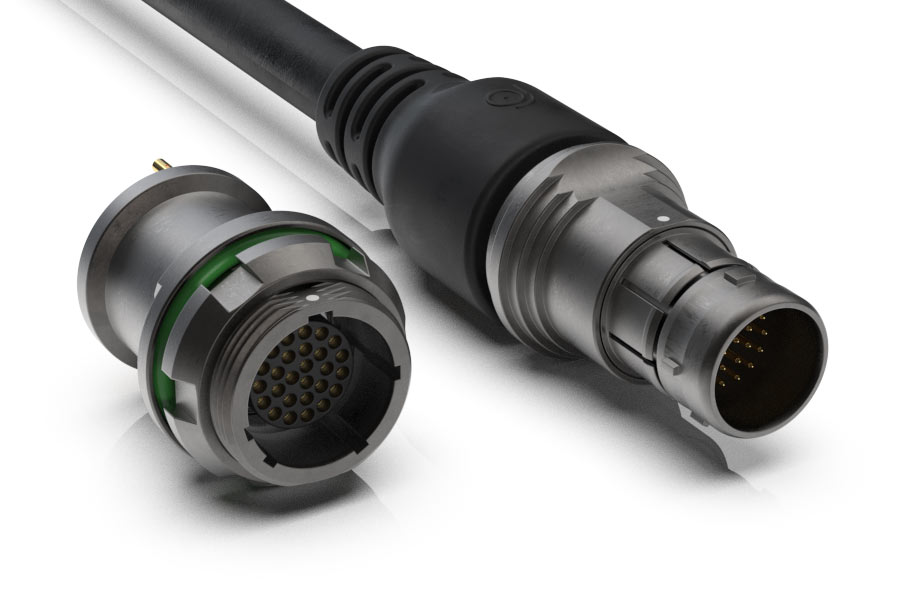
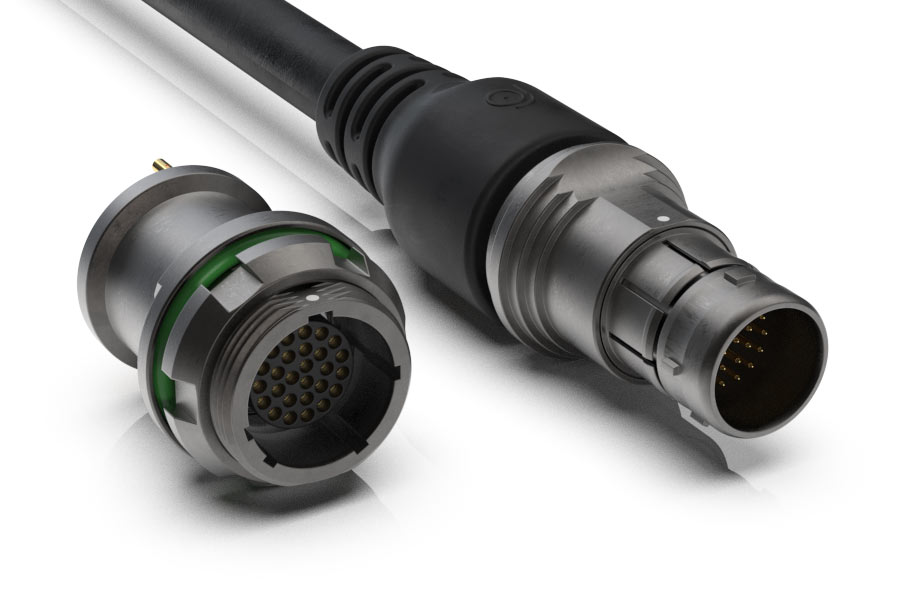
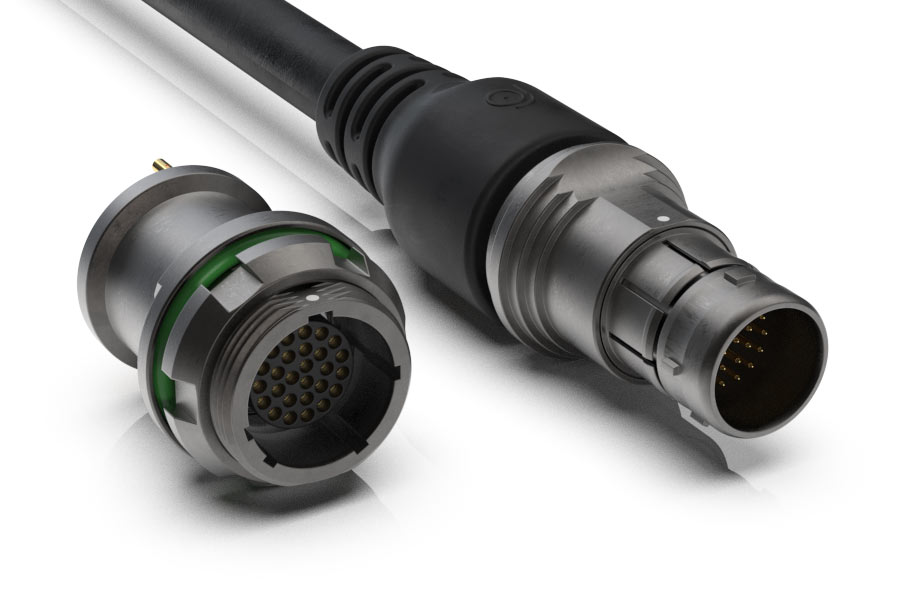
Sealing is a very complex science itself, as it involves many physical aspects including mechanical design, materials science, surface science, and fluid behavior.
Hermeticity is one of the toughest challenges that design engineers face when specifying the connectors needed for their device, since their applications require the tightest sealing that will not just keep dust and water out but will provide a barrier to gases down to the molecular level, i.e., gas tightness.
Sealing is a very complex science itself, as it involves many physical aspects including mechanical design, materials science, surface science, and fluid behavior.
Hermeticity is one of the toughest challenges that design engineers face when specifying the connectors needed for their device, since their applications require the tightest sealing that will not just keep dust and water out but will provide a barrier to gases down to the molecular level, i.e., gas tightness.
Sealing is a very complex science itself, as it involves many physical aspects including mechanical design, materials science, surface science, and fluid behavior.
Hermeticity is one of the toughest challenges that design engineers face when specifying the connectors needed for their device, since their applications require the tightest sealing that will not just keep dust and water out but will provide a barrier to gases down to the molecular level, i.e., gas tightness.
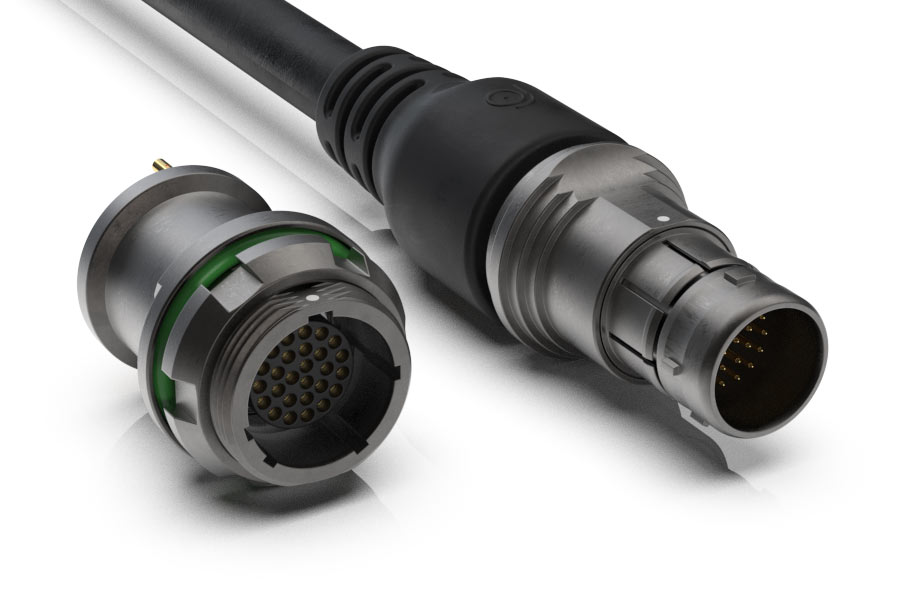
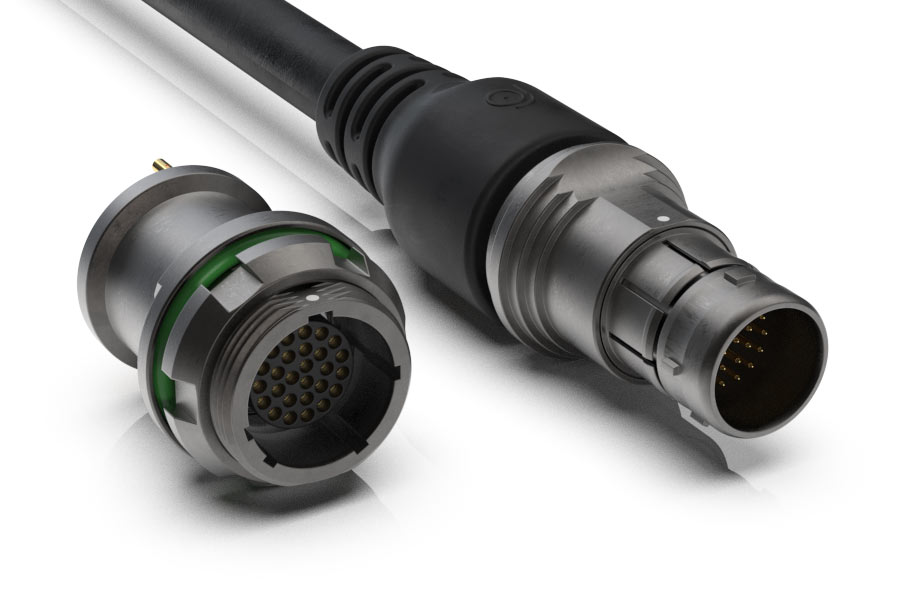
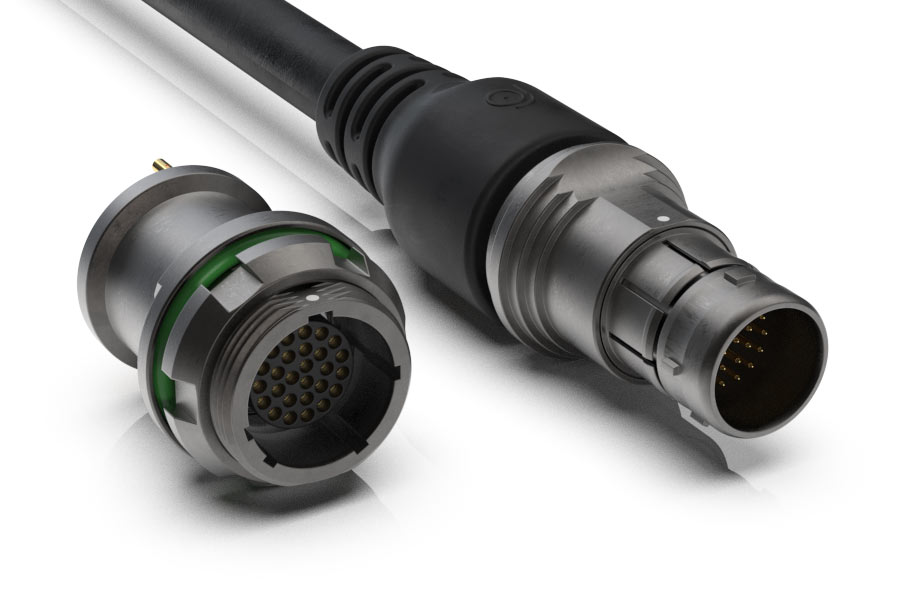
Sealing is a very complex science itself, as it involves many physical aspects including mechanical design, materials science, surface science, and fluid behavior.
Hermeticity is one of the toughest challenges that design engineers face when specifying the connectors needed for their device, since their applications require the tightest sealing that will not just keep dust and water out but will provide a barrier to gases down to the molecular level, i.e., gas tightness.
Sealing is a very complex science itself, as it involves many physical aspects including mechanical design, materials science, surface science, and fluid behavior.
Hermeticity is one of the toughest challenges that design engineers face when specifying the connectors needed for their device, since their applications require the tightest sealing that will not just keep dust and water out but will provide a barrier to gases down to the molecular level, i.e., gas tightness.
Sealing is a very complex science itself, as it involves many physical aspects including mechanical design, materials science, surface science, and fluid behavior.
Hermeticity is one of the toughest challenges that design engineers face when specifying the connectors needed for their device, since their applications require the tightest sealing that will not just keep dust and water out but will provide a barrier to gases down to the molecular level, i.e., gas tightness.
Sales request
Get STEP files and product information
Our hermetic connector solutions
Our hermetically sealed connectivity solutions are well-known not only for their reliability but also for their long lifespan and durability.
Fischer Connectors’ founder, Walter Werner Fischer, developed the world’s first high-quality sealed connector for use in industrial applications in the ‘50s, and the first hermetic feedthrough connector for a vacuum chamber in 1964. No wonder that hermeticity is one of our flagship technologies, making our company brand, in the eyes of design engineers worldwide, synonymous with high-reliability connectivity in demanding and harsh environments.
Engineers designing applications requiring high-hermiticity performance choose gas-tight connectors from our high-performance product range.
Our hermetically sealed connectivity solutions are well-known not only for their reliability but also for their long lifespan and durability.
Fischer Connectors’ founder, Walter Werner Fischer, developed the world’s first high-quality sealed connector for use in industrial applications in the ‘50s, and the first hermetic feedthrough connector for a vacuum chamber in 1964. No wonder that hermeticity is one of our flagship technologies, making our company brand, in the eyes of design engineers worldwide, synonymous with high-reliability connectivity in demanding and harsh environments.
Engineers designing applications requiring high-hermiticity performance choose gas-tight connectors from our high-performance product range.
Our hermetically sealed connectivity solutions are well-known not only for their reliability but also for their long lifespan and durability.
Fischer Connectors’ founder, Walter Werner Fischer, developed the world’s first high-quality sealed connector for use in industrial applications in the ‘50s, and the first hermetic feedthrough connector for a vacuum chamber in 1964. No wonder that hermeticity is one of our flagship technologies, making our company brand, in the eyes of design engineers worldwide, synonymous with high-reliability connectivity in demanding and harsh environments.
Engineers designing applications requiring high-hermiticity performance choose gas-tight connectors from our high-performance product range.
Key features
- Designed and tested to ensure a leak smaller than 10-8 mbar l/s per IEC 60068-2-17, covering gas-tightness needs from low to ultra-high vacuum levels
- Ultra-reliable functionality, long lifespan and durability
- Technical support and assistance
- Solutions tailored to your needs and in line with the most stringent standards of your industry
Our R&D department conducts risk analyses to assist customers in selecting solutions with the appropriate level of hermetic sealing to match the specific influences and conditions in which their device operates.
Our R&D department conducts risk analyses to assist customers in selecting solutions with the appropriate level of hermetic sealing to match the specific influences and conditions in which their device operates.
Our R&D department conducts risk analyses to assist customers in selecting solutions with the appropriate level of hermetic sealing to match the specific influences and conditions in which their device operates.
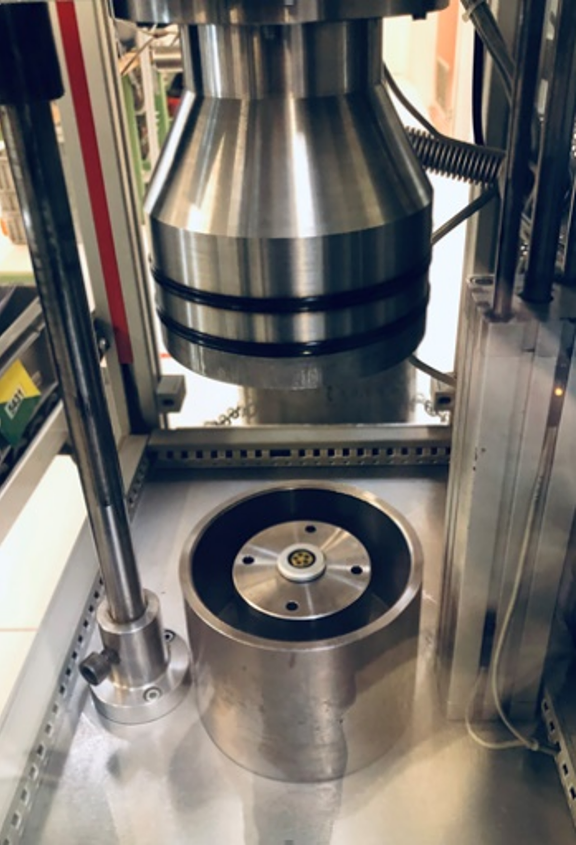
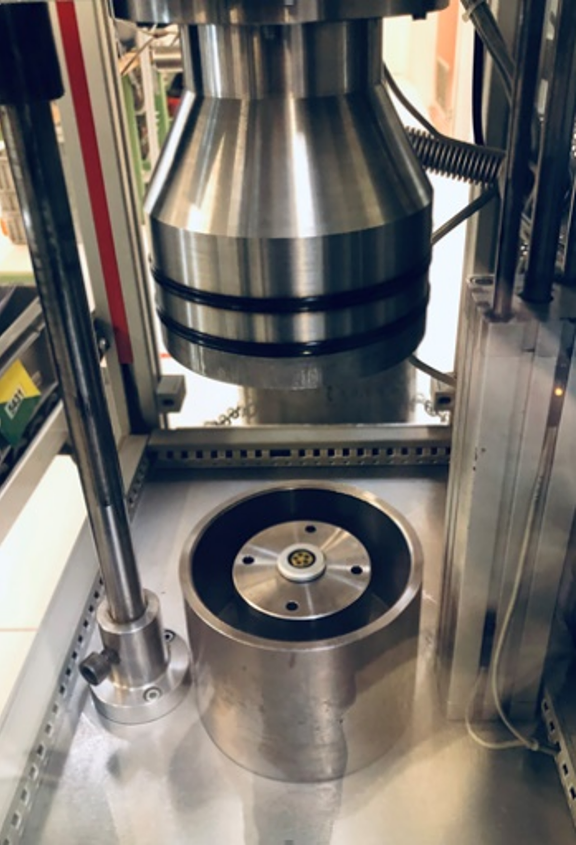
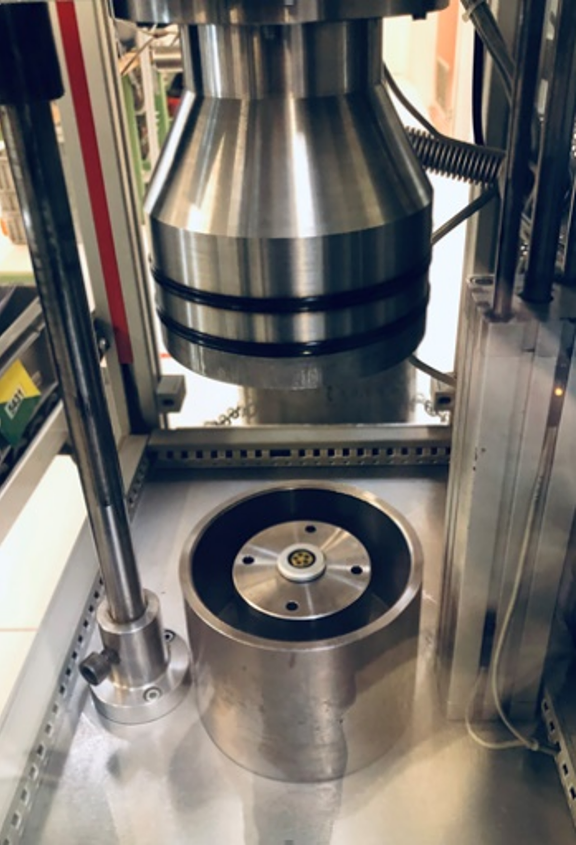
Our product range
Our product range
Our product range
Need other features?
Our custom connector capabilities will help you meet your needs.
Learn more about hermetically sealed connectors
Hermetic sealing is required for gas tightness, e.g., in vacuum applications or pressurized vessels. These applications require a high level of sealing to prevent gas leaks over longer periods. Gas-tight connectors or vacuum-tight connectors are designed specifically for hermetic sealing and undergo a 100% leak test. Hermetic interconnects are also needed for devices immersed for longer periods of time or exposed to strong water jets.
Hermetic sealing is required for gas tightness, e.g., in vacuum applications or pressurized vessels. These applications require a high level of sealing to prevent gas leaks over longer periods. Gas-tight connectors or vacuum-tight connectors are designed specifically for hermetic sealing and undergo a 100% leak test. Hermetic interconnects are also needed for devices immersed for longer periods of time or exposed to strong water jets.
Hermetic sealing is required for gas tightness, e.g., in vacuum applications or pressurized vessels. These applications require a high level of sealing to prevent gas leaks over longer periods. Gas-tight connectors or vacuum-tight connectors are designed specifically for hermetic sealing and undergo a 100% leak test. Hermetic interconnects are also needed for devices immersed for longer periods of time or exposed to strong water jets.
For applications requiring exposure for extended periods of time in liquids under high pressure, e.g., deep-submarine applications or drilling instrumentation used in oil & gas, special designs are proposed that combine hermetic sealing with resistance to high mechanical strength.
For applications requiring exposure for extended periods of time in liquids under high pressure, e.g., deep-submarine applications or drilling instrumentation used in oil & gas, special designs are proposed that combine hermetic sealing with resistance to high mechanical strength.
For applications requiring exposure for extended periods of time in liquids under high pressure, e.g., deep-submarine applications or drilling instrumentation used in oil & gas, special designs are proposed that combine hermetic sealing with resistance to high mechanical strength.
Tips to choose the right hermetic connector
Tips to choose the right hermetic connector
Tips to choose the right hermetic connector
In order to successfully specify an airtight, hermetically sealed connector, it is important to understand the function of the specific vacuum application and how hermetic connectors should be manufactured to minimize or stop gases from leaking into or out of the vacuum chamber. Specifications to consider include :
In order to successfully specify an airtight, hermetically sealed connector, it is important to understand the function of the specific vacuum application and how hermetic connectors should be manufactured to minimize or stop gases from leaking into or out of the vacuum chamber. Specifications to consider include :
In order to successfully specify an airtight, hermetically sealed connector, it is important to understand the function of the specific vacuum application and how hermetic connectors should be manufactured to minimize or stop gases from leaking into or out of the vacuum chamber. Specifications to consider include :
Vacuum level & pressure gradient
Depending on the application, different vacuum levels must be achieved within the chamber, so check the specific vacuum level required for your device. 10 mbar is defined as ‘low vacuum’, 1E-5 mbar as ‘high vacuum’ and 1E-7 mbar as ‘ultra-high vacuum’. As a reminder, ‘atmospheric’ pressure is equal to one bar = 1000 millibars (1000mbar).
Gas type
Measure the hermetic connector leak according to gas type. The most common leak-measurement equipment is the ‘helium tracer’. As all vacuum applications do not work with helium, the leak can be given for air molecules. Air leaks ‘2.6 times less’ than helium. This means that if a hermetic connector leak is measured as 4E-7 mbar l/s under a helium atmosphere, the real vacuum application (air) will have a leak of 1.5E-7 mbar l/s.
O-ring material
Identify and select the proper material for O-rings to prevent unwanted permeation or diffusion effects. Diffusion occurs in most plastics and rubber materials, allowing extremely small quantities of gas to migrate through the hermetic barrier.
This can happen when the O-ring is exposed to a pressure gradient allowing gas molecules (nitrogen, helium, oxygen) to progressively go slowly, or ‘diffuse’ into the O-ring and out of the other side.
The diffusion ‘leak’ is difficult to measure because there is no single measurement point in the O-ring material sealing the hermetic connector. That is why components such as hermetic connectors or other devices mounted on hermetic systems will exhibit a residual leakage resulting from gas diffusion through the sealing material. The optimized design of these components and adequate material selection allows the residual leakage rate to remain at extremely low values, suitable for most ultra-vacuum applications.
Vacuum level & pressure gradient
Depending on the application, different vacuum levels must be achieved within the chamber, so check the specific vacuum level required for your device. 10 mbar is defined as ‘low vacuum’, 1E-5 mbar as ‘high vacuum’ and 1E-7 mbar as ‘ultra-high vacuum’. As a reminder, ‘atmospheric’ pressure is equal to one bar = 1000 millibars (1000mbar).
Gas type
Measure the hermetic connector leak according to gas type. The most common leak-measurement equipment is the ‘helium tracer’. As all vacuum applications do not work with helium, the leak can be given for air molecules. Air leaks ‘2.6 times less’ than helium. This means that if a hermetic connector leak is measured as 4E-7 mbar l/s under a helium atmosphere, the real vacuum application (air) will have a leak of 1.5E-7 mbar l/s.
O-ring material
Identify and select the proper material for O-rings to prevent unwanted permeation or diffusion effects. Diffusion occurs in most plastics and rubber materials, allowing extremely small quantities of gas to migrate through the hermetic barrier.
This can happen when the O-ring is exposed to a pressure gradient allowing gas molecules (nitrogen, helium, oxygen) to progressively go slowly, or ‘diffuse’ into the O-ring and out of the other side.
The diffusion ‘leak’ is difficult to measure because there is no single measurement point in the O-ring material sealing the hermetic connector. That is why components such as hermetic connectors or other devices mounted on hermetic systems will exhibit a residual leakage resulting from gas diffusion through the sealing material. The optimized design of these components and adequate material selection allows the residual leakage rate to remain at extremely low values, suitable for most ultra-vacuum applications.
Vacuum level & pressure gradient
Depending on the application, different vacuum levels must be achieved within the chamber, so check the specific vacuum level required for your device. 10 mbar is defined as ‘low vacuum’, 1E-5 mbar as ‘high vacuum’ and 1E-7 mbar as ‘ultra-high vacuum’. As a reminder, ‘atmospheric’ pressure is equal to one bar = 1000 millibars (1000mbar).
Gas type
Measure the hermetic connector leak according to gas type. The most common leak-measurement equipment is the ‘helium tracer’. As all vacuum applications do not work with helium, the leak can be given for air molecules. Air leaks ‘2.6 times less’ than helium. This means that if a hermetic connector leak is measured as 4E-7 mbar l/s under a helium atmosphere, the real vacuum application (air) will have a leak of 1.5E-7 mbar l/s.
O-ring material
Identify and select the proper material for O-rings to prevent unwanted permeation or diffusion effects. Diffusion occurs in most plastics and rubber materials, allowing extremely small quantities of gas to migrate through the hermetic barrier.
This can happen when the O-ring is exposed to a pressure gradient allowing gas molecules (nitrogen, helium, oxygen) to progressively go slowly, or ‘diffuse’ into the O-ring and out of the other side.
The diffusion ‘leak’ is difficult to measure because there is no single measurement point in the O-ring material sealing the hermetic connector. That is why components such as hermetic connectors or other devices mounted on hermetic systems will exhibit a residual leakage resulting from gas diffusion through the sealing material. The optimized design of these components and adequate material selection allows the residual leakage rate to remain at extremely low values, suitable for most ultra-vacuum applications.
Connector material
Seawater and salt mist can act as an electrolyte because salt water strongly increases its conductivity, enabling galvanic corrosion effects to occur. Choose the right materials and coatings for your connectivity solutions to resist corrosion in your underwater and marine applications. Fischer Connectors’ hermetic products are tested through long-standing exposure to a 5% salt solution at a temperature of 35°C without any impact on their mechanical or electrical functionalities. They are available in a wide choice of materials and coatings to ensure their resistance to corrosion in salt and marine environments:
Connector material
Seawater and salt mist can act as an electrolyte because salt water strongly increases its conductivity, enabling galvanic corrosion effects to occur. Choose the right materials and coatings for your connectivity solutions to resist corrosion in your underwater and marine applications. Fischer Connectors’ hermetic products are tested through long-standing exposure to a 5% salt solution at a temperature of 35°C without any impact on their mechanical or electrical functionalities. They are available in a wide choice of materials and coatings to ensure their resistance to corrosion in salt and marine environments:
Connector material
Seawater and salt mist can act as an electrolyte because salt water strongly increases its conductivity, enabling galvanic corrosion effects to occur. Choose the right materials and coatings for your connectivity solutions to resist corrosion in your underwater and marine applications. Fischer Connectors’ hermetic products are tested through long-standing exposure to a 5% salt solution at a temperature of 35°C without any impact on their mechanical or electrical functionalities. They are available in a wide choice of materials and coatings to ensure their resistance to corrosion in salt and marine environments:
Recommended product line | Raw material | Coating |
Fischer Core Series Brass | Brass | Ni + Cr |
Fischer Core Series Stainless Steel | Stainless steel 316L | Uncoated |
Fischer UltiMate™ Series | Brass | Ni |
Fischer FiberOptic Series | Brass | Ni + Cr |
Fischer MiniMax™ Series | Brass | Ni + Cr |
Fischer Freedom™ Series | Brass/Stainless steel | Ni |
Recommended product line | Raw material | Coating |
Fischer Core Series Brass | Brass | Ni + Cr |
Fischer Core Series Stainless Steel | Stainless steel 316L | Uncoated |
Fischer UltiMate™ Series | Brass | Ni |
Fischer FiberOptic Series | Brass | Ni + Cr |
Fischer MiniMax™ Series | Brass | Ni + Cr |
Fischer Freedom™ Series | Brass/Stainless steel | Ni |
Recommended product line | Raw material | Coating |
Fischer Core Series Brass | Brass | Ni + Cr |
Fischer Core Series Stainless Steel | Stainless steel 316L | Uncoated |
Fischer UltiMate™ Series | Brass | Ni |
Fischer FiberOptic Series | Brass | Ni + Cr |
Fischer MiniMax™ Series | Brass | Ni + Cr |
Fischer Freedom™ Series | Brass/Stainless steel | Ni |
Body style
The choice of receptacle body styles depends on how IP69 connectors or hermetic connectors are mounted onto the panel. Hermeticity for best sealing under high pressures is achieved through a specific O-ring and sealing material (epoxy compound).
The body styles of our hermetic bulkhead feedthrough connectors (see illustration below) are specially designed to allow the passing of electrical signals and power through a panel via two cabled plugs.
Body style
The choice of receptacle body styles depends on how IP69 connectors or hermetic connectors are mounted onto the panel. Hermeticity for best sealing under high pressures is achieved through a specific O-ring and sealing material (epoxy compound).
The body styles of our hermetic bulkhead feedthrough connectors (see illustration below) are specially designed to allow the passing of electrical signals and power through a panel via two cabled plugs.
Body style
The choice of receptacle body styles depends on how IP69 connectors or hermetic connectors are mounted onto the panel. Hermeticity for best sealing under high pressures is achieved through a specific O-ring and sealing material (epoxy compound).
The body styles of our hermetic bulkhead feedthrough connectors (see illustration below) are specially designed to allow the passing of electrical signals and power through a panel via two cabled plugs.
Examples of high-performance hermetic connector applications
Hermetic connectors are critical to the functional integrity and durability of a multitude of devices and applications operating in harsh, hazardous, or pressurized environments such as aerospace, defense, instrumentation, oil & gas, and underwater equipment, both military and civil.
Hermetic connectors are critical to the functional integrity and durability of a multitude of devices and applications operating in harsh, hazardous, or pressurized environments such as aerospace, defense, instrumentation, oil & gas, and underwater equipment, both military and civil.
Hermetic connectors are critical to the functional integrity and durability of a multitude of devices and applications operating in harsh, hazardous, or pressurized environments such as aerospace, defense, instrumentation, oil & gas, and underwater equipment, both military and civil.
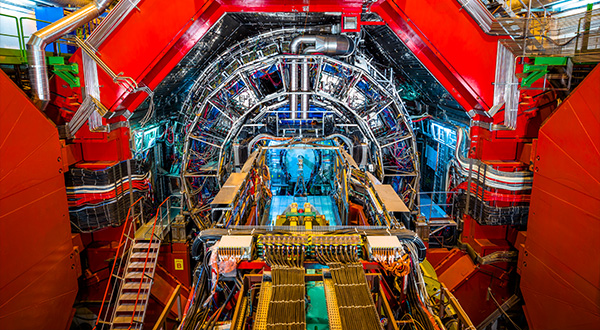
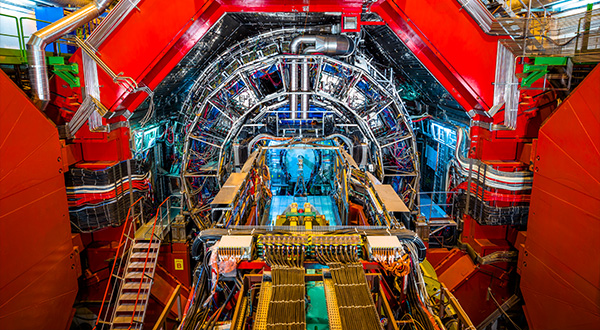
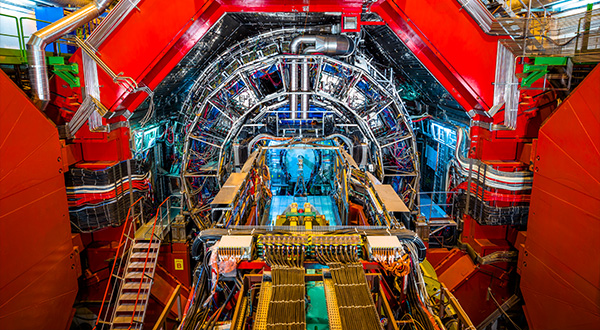
Scientific researches
Hermetic connectors are typically used for pressurized vessels, test & measurement tools like mass spectrometers and electron microscopes, and vacuum applications such as vacuum pumps and chambers for monitoring and safety devices in nuclear research.
For example at the CERN, whose various equipment and devices have been using our gas-tight connectivity solutions for decades.
Scientific researches
Hermetic connectors are typically used for pressurized vessels, test & measurement tools like mass spectrometers and electron microscopes, and vacuum applications such as vacuum pumps and chambers for monitoring and safety devices in nuclear research.
For example at the CERN, whose various equipment and devices have been using our gas-tight connectivity solutions for decades.
Scientific researches
Hermetic connectors are typically used for pressurized vessels, test & measurement tools like mass spectrometers and electron microscopes, and vacuum applications such as vacuum pumps and chambers for monitoring and safety devices in nuclear research.
For example at the CERN, whose various equipment and devices have been using our gas-tight connectivity solutions for decades.
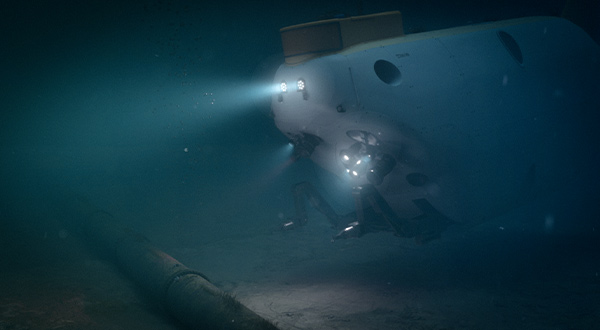
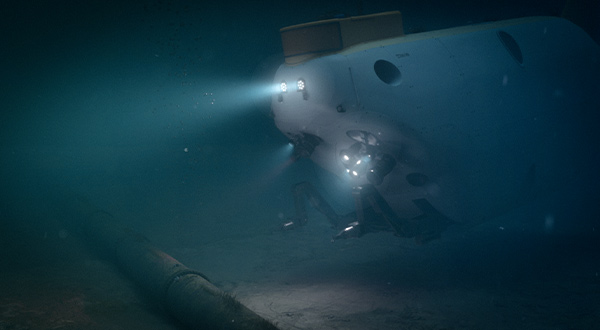
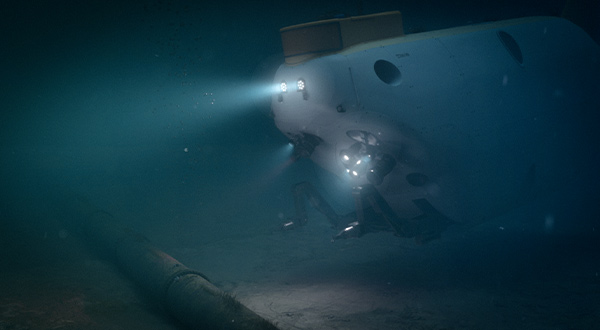
Deep-submarine
Deep-submarine applications such as thickness-measurement instruments for pipeline inspection, as well as seismic-evaluation and drilling instruments in the oil & gas sector, are exposed for extended periods of time to liquids under high pressure.
The hermetic connectors they use are specially engineered to combine hermetic sealing with high-strength mechanical design.
Deep-submarine
Deep-submarine applications such as thickness-measurement instruments for pipeline inspection, as well as seismic-evaluation and drilling instruments in the oil & gas sector, are exposed for extended periods of time to liquids under high pressure.
The hermetic connectors they use are specially engineered to combine hermetic sealing with high-strength mechanical design.
Deep-submarine
Deep-submarine applications such as thickness-measurement instruments for pipeline inspection, as well as seismic-evaluation and drilling instruments in the oil & gas sector, are exposed for extended periods of time to liquids under high pressure.
The hermetic connectors they use are specially engineered to combine hermetic sealing with high-strength mechanical design.
Hermeticity explained
Gas tightness
Hermeticity is one of the toughest challenges for manufacturers of devices with a vacuum chamber or pressurized vessels.
Such applications require the tightest sealing that not only keeps dust and water out, but also provides a barrier to gases down to the molecular level – gas tightness.
Making it work properly
A vacuum is made when gas molecules are taken out of a chamber. To achieve specific physical reactions, a vacuum has to be created in a chamber so that air molecules will act as a barrier for other molecules or electrons. For example, a mass spectrometer needs a vacuum chamber to work properly, but it also needs a hermetic connector so that the measurements can be recorded accurately.
If a connector is placed on the vacuum chamber, the air going through the connector over time must be as small as possible. The connector has to be ‘hermetic’, in that it does not allow air molecules to enter the vacuum chamber. If the connector is not hermetic, it will allow air into the vacuum chamber, which will increase the residual pressure and prevent the equipment from working properly.
Gas tightness
Hermeticity is one of the toughest challenges for manufacturers of devices with a vacuum chamber or pressurized vessels.
Such applications require the tightest sealing that not only keeps dust and water out, but also provides a barrier to gases down to the molecular level – gas tightness.
Making it work properly
A vacuum is made when gas molecules are taken out of a chamber. To achieve specific physical reactions, a vacuum has to be created in a chamber so that air molecules will act as a barrier for other molecules or electrons. For example, a mass spectrometer needs a vacuum chamber to work properly, but it also needs a hermetic connector so that the measurements can be recorded accurately.
If a connector is placed on the vacuum chamber, the air going through the connector over time must be as small as possible. The connector has to be ‘hermetic’, in that it does not allow air molecules to enter the vacuum chamber. If the connector is not hermetic, it will allow air into the vacuum chamber, which will increase the residual pressure and prevent the equipment from working properly.
Gas tightness
Hermeticity is one of the toughest challenges for manufacturers of devices with a vacuum chamber or pressurized vessels.
Such applications require the tightest sealing that not only keeps dust and water out, but also provides a barrier to gases down to the molecular level – gas tightness.
Making it work properly
A vacuum is made when gas molecules are taken out of a chamber. To achieve specific physical reactions, a vacuum has to be created in a chamber so that air molecules will act as a barrier for other molecules or electrons. For example, a mass spectrometer needs a vacuum chamber to work properly, but it also needs a hermetic connector so that the measurements can be recorded accurately.
If a connector is placed on the vacuum chamber, the air going through the connector over time must be as small as possible. The connector has to be ‘hermetic’, in that it does not allow air molecules to enter the vacuum chamber. If the connector is not hermetic, it will allow air into the vacuum chamber, which will increase the residual pressure and prevent the equipment from working properly.
Leak unit
A quantity of air (or other gas) going through a hermetic connector is a leak. In order to quantify a leak, the leak unit is based on a ‘certain volume of gas per second going through it’. The scientific unit is mbar l/s, i.e., the amount of gas necessary to be removed from a one-liter container in one second to reduce the pressure by one millibar.
In the vacuum industry, 5E-7 mbar l/s is considered a very small leak that will not impair most vacuum applications. 1E-4 mbar l/s is considered a ‘big leak’, and only very rare low-vacuum applications can afford such a leak in the vacuum chamber.
Leak unit
A quantity of air (or other gas) going through a hermetic connector is a leak. In order to quantify a leak, the leak unit is based on a ‘certain volume of gas per second going through it’. The scientific unit is mbar l/s, i.e., the amount of gas necessary to be removed from a one-liter container in one second to reduce the pressure by one millibar.
In the vacuum industry, 5E-7 mbar l/s is considered a very small leak that will not impair most vacuum applications. 1E-4 mbar l/s is considered a ‘big leak’, and only very rare low-vacuum applications can afford such a leak in the vacuum chamber.
Leak unit
A quantity of air (or other gas) going through a hermetic connector is a leak. In order to quantify a leak, the leak unit is based on a ‘certain volume of gas per second going through it’. The scientific unit is mbar l/s, i.e., the amount of gas necessary to be removed from a one-liter container in one second to reduce the pressure by one millibar.
In the vacuum industry, 5E-7 mbar l/s is considered a very small leak that will not impair most vacuum applications. 1E-4 mbar l/s is considered a ‘big leak’, and only very rare low-vacuum applications can afford such a leak in the vacuum chamber.
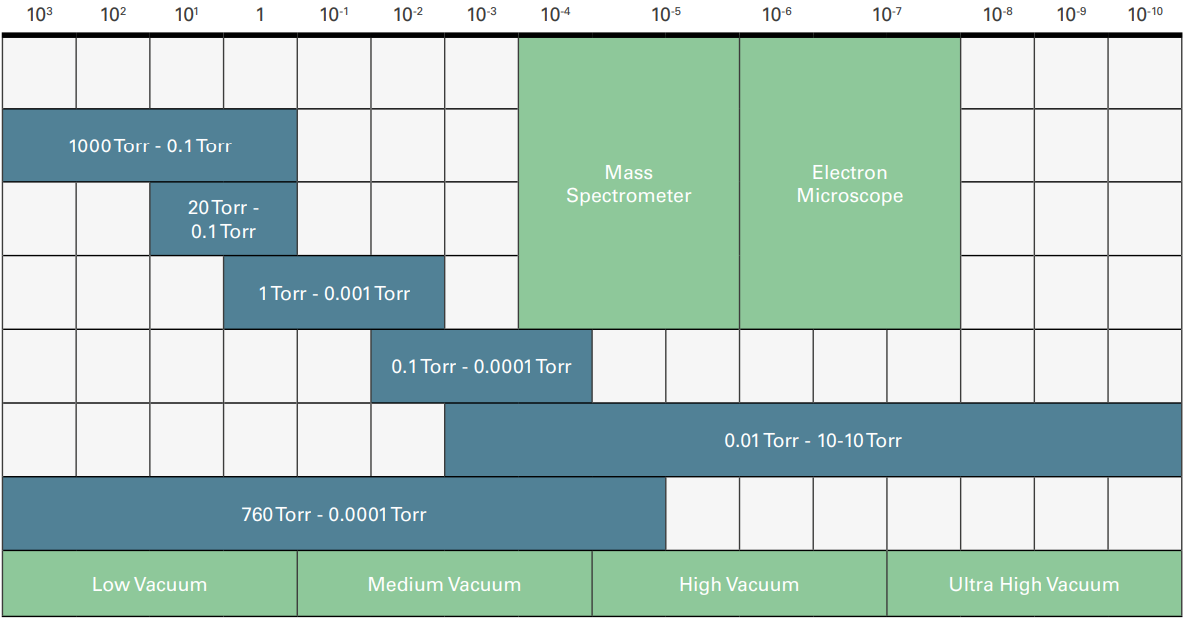
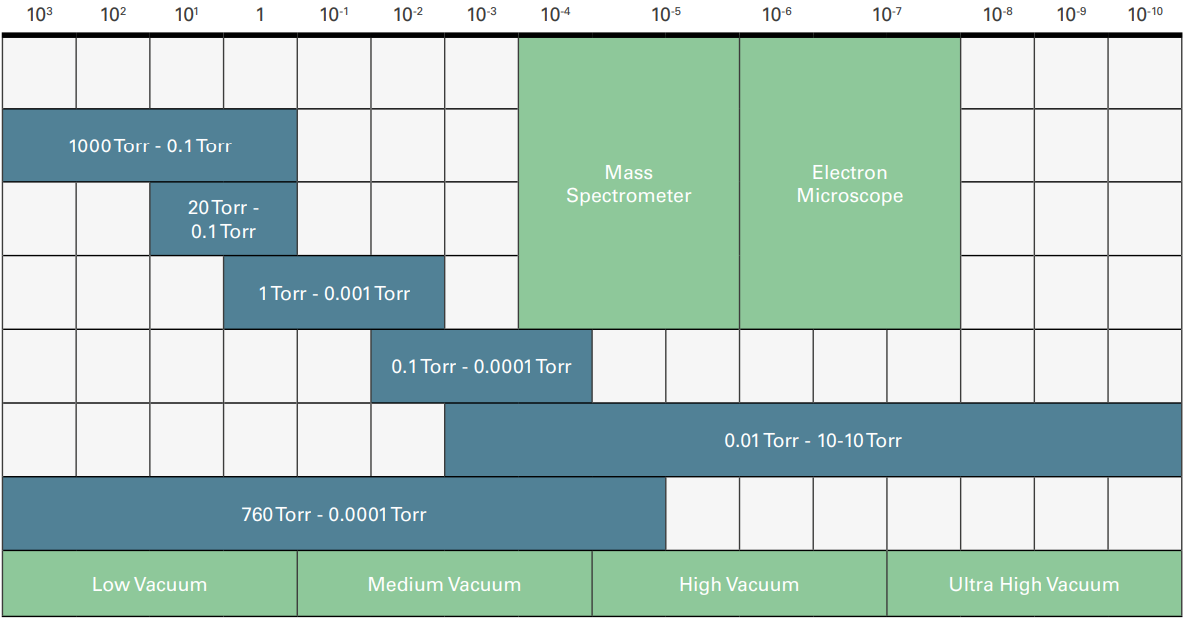
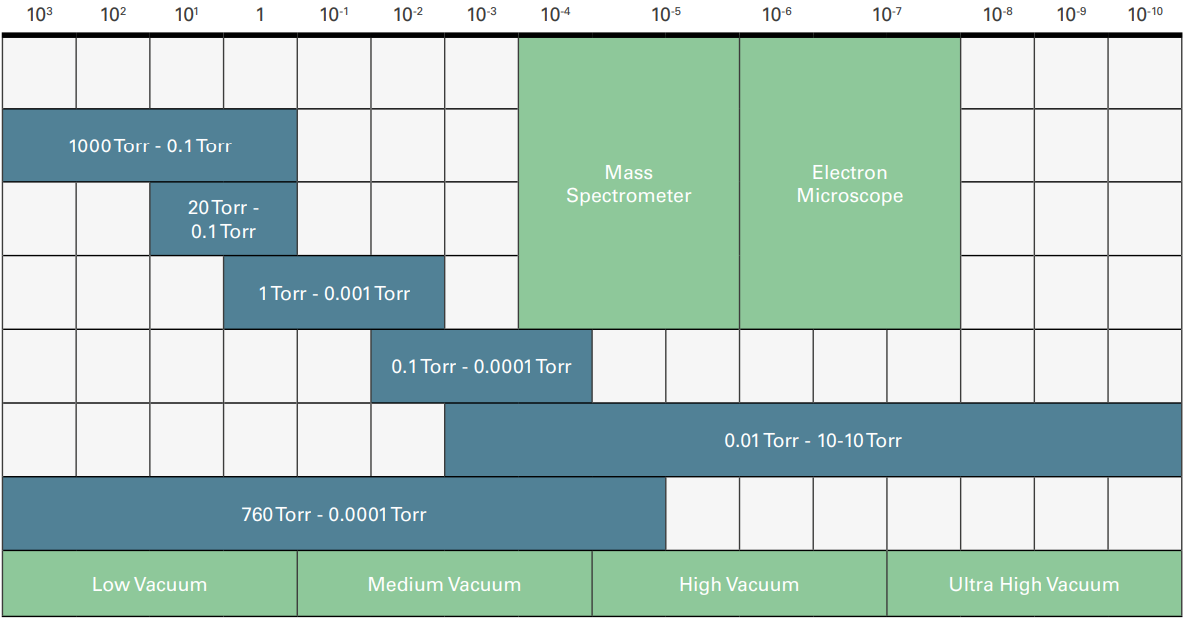